EAGAN, Minn. —Mark Miller isn't donning pads or a coach's whistle anytime soon.
But he is putting himself in the shoes of the Vikings.
Miller is a Senior Project Manager with Minneapolis-based Kraus-Anderson Construction, which has made tremendous progress on Twin Cities Orthopedics Performance Center in less than a year from the pouring of the first footing.
The Vikings future headquarters is scheduled for completion on March 1.
Miller has worked with architects, subcontractors and Vikings representatives to bring the design to fruition and manage any changes of plans.
While the task involves a heavy dose of meetings and coordination of supplies and workers, Miller most enjoys walking the site about every other day and visualizing how the facility will benefit players, coaches and staff.
Although the TCO Performance Center was much less complete in May than its current 70-percent-completion status, Miller enjoyed gaining perspective from Stefon Diggs when the Vikings receiver stopped by more than six months ago.
Vikings wide receiver Stefon Diggs took a trip to Eagan as the final steel beam was installed and toured the future home of the Minnesota Vikings, the Twin Cities Orthopedics Performance Center.
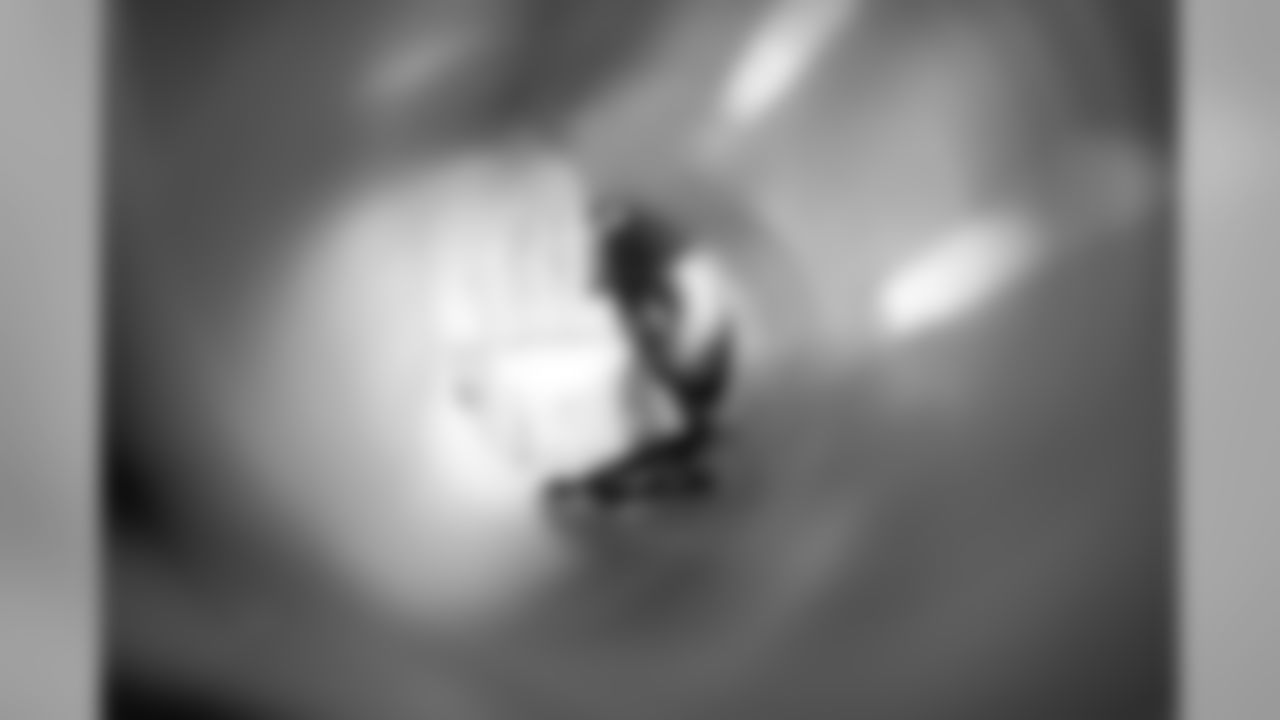
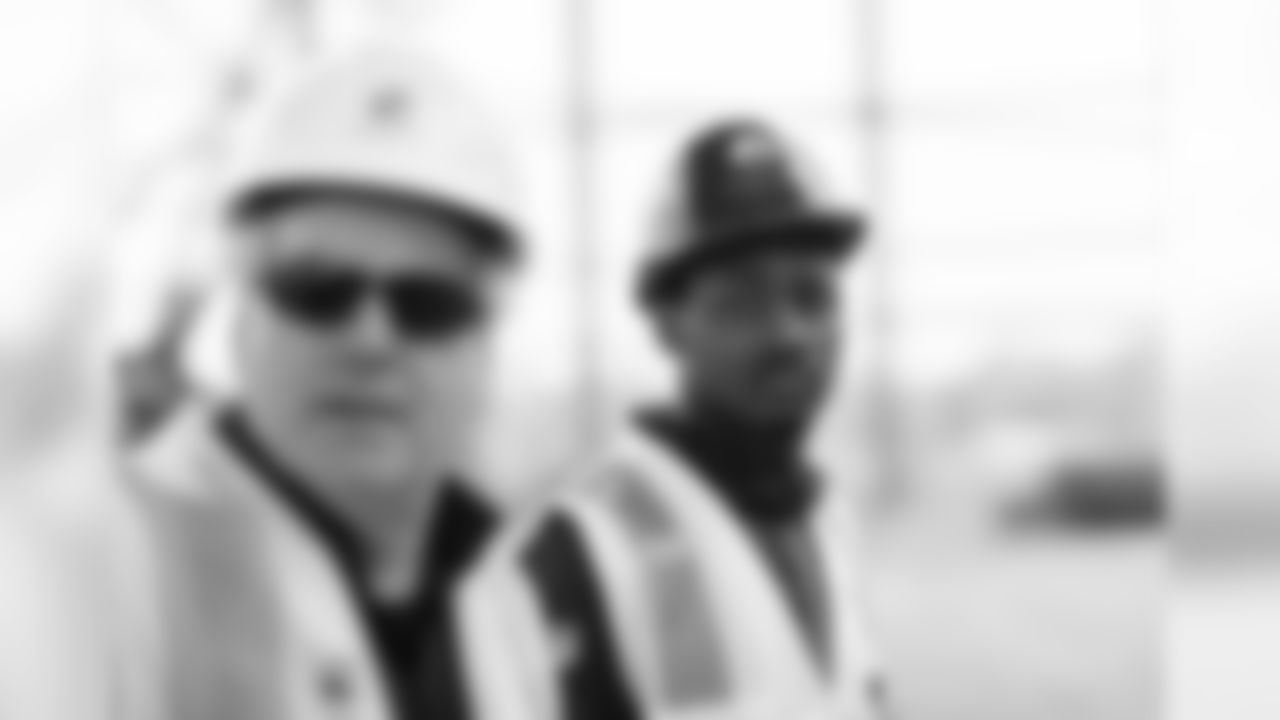
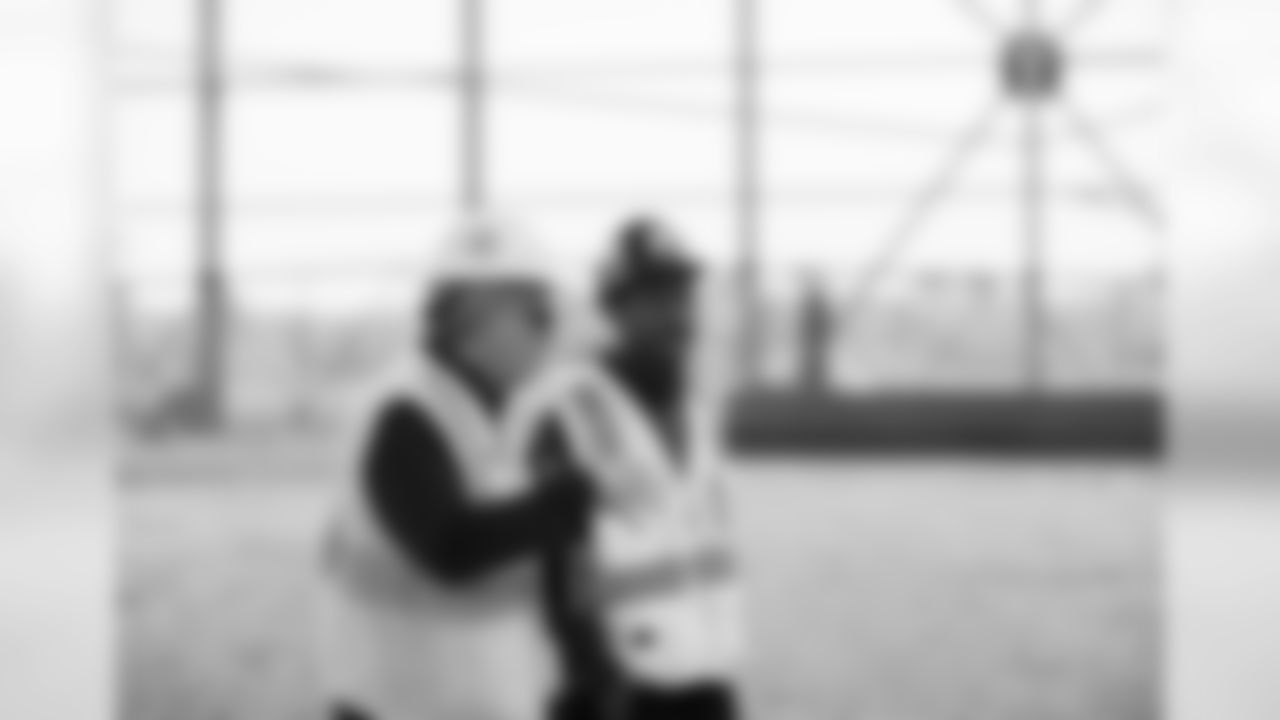
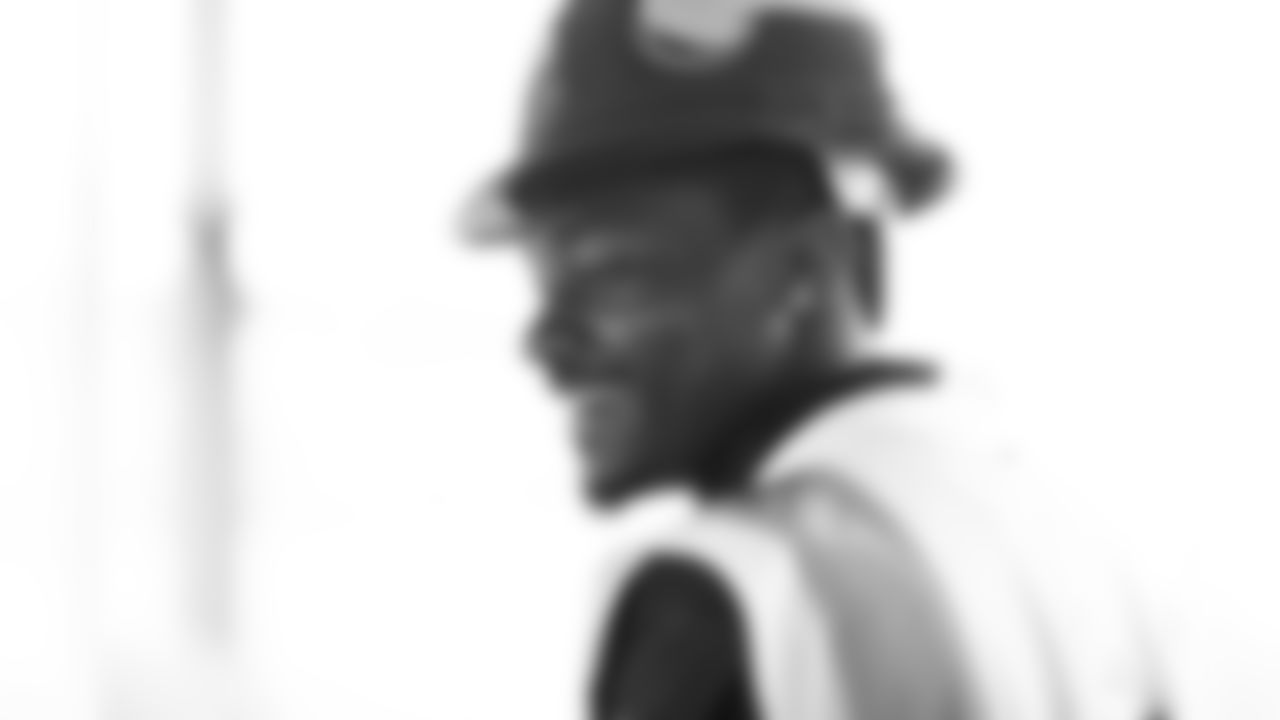
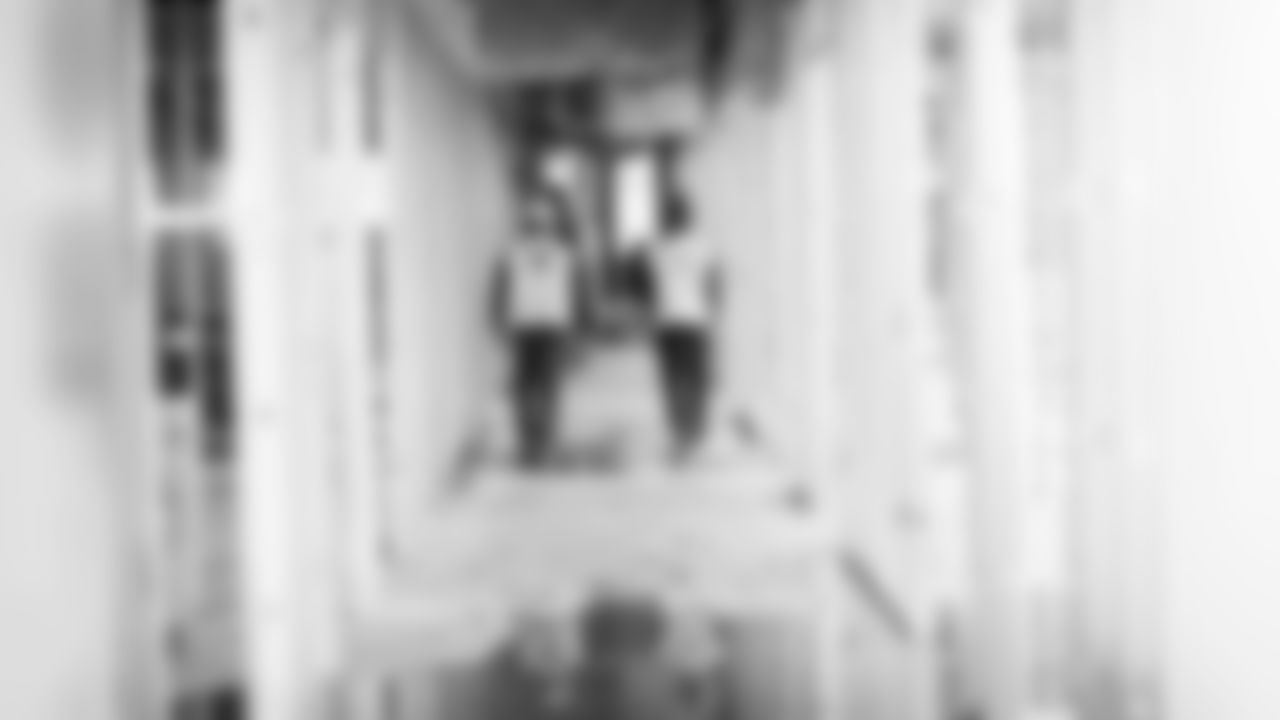
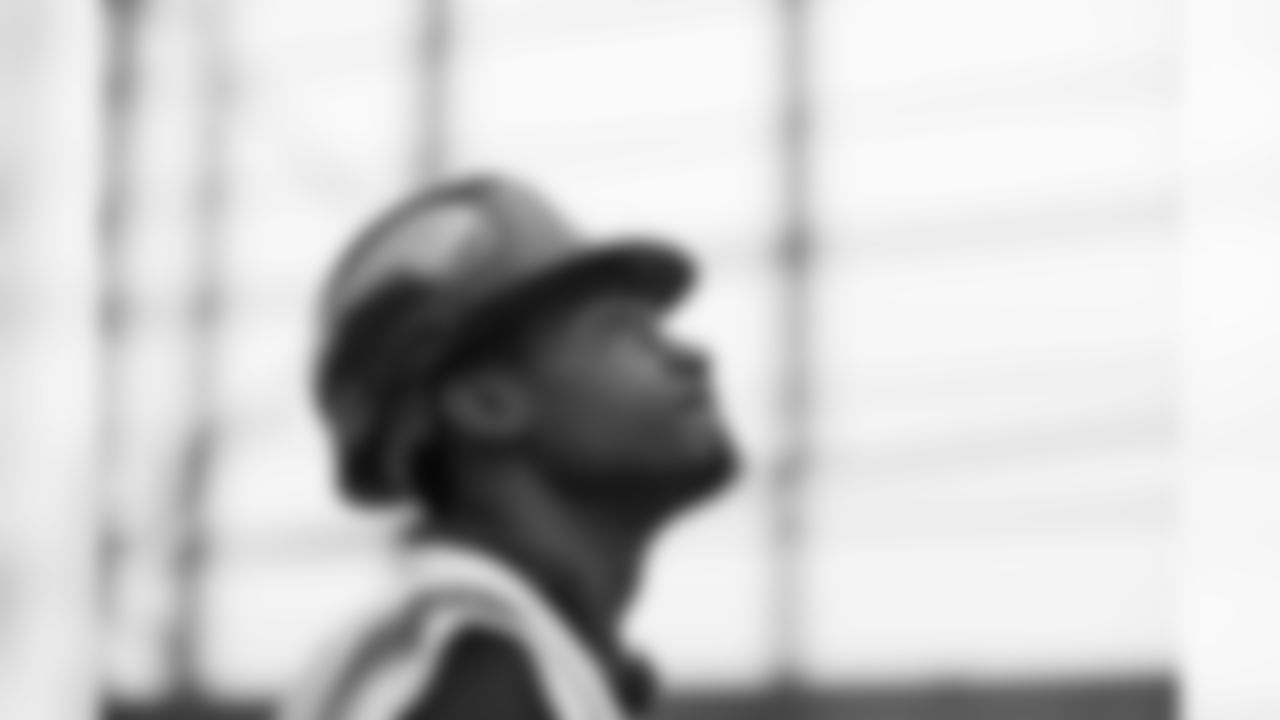
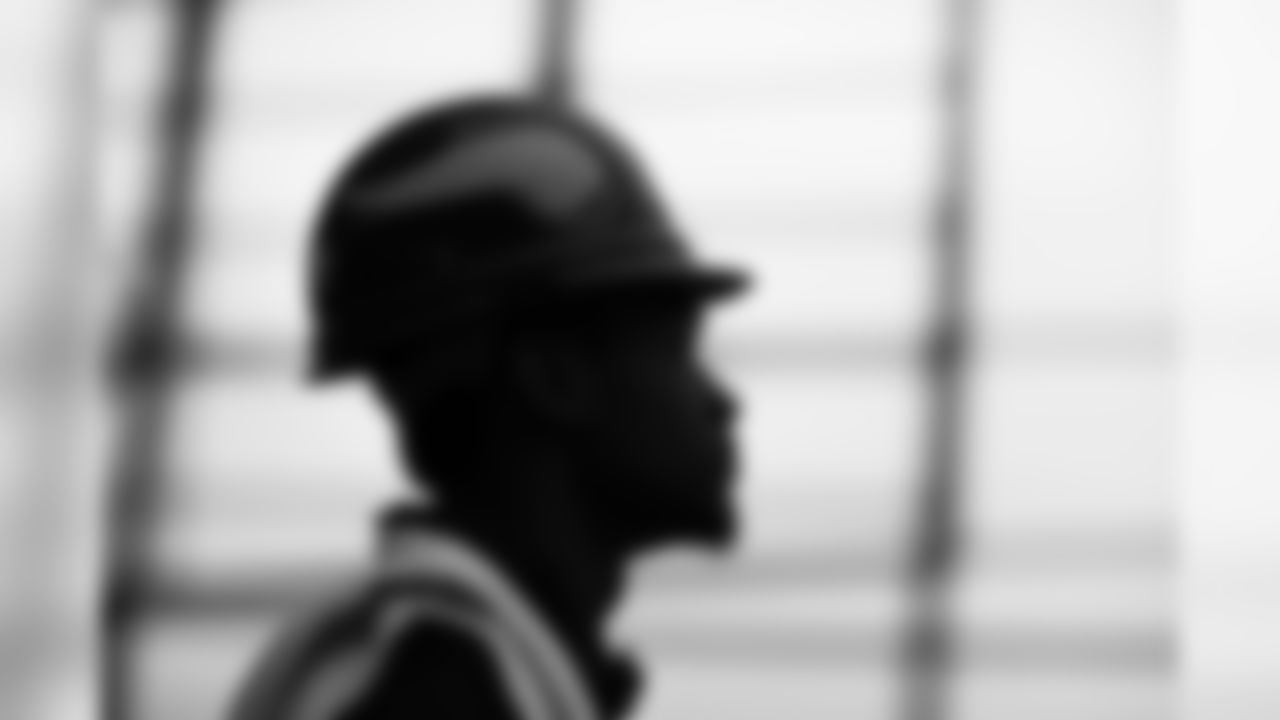
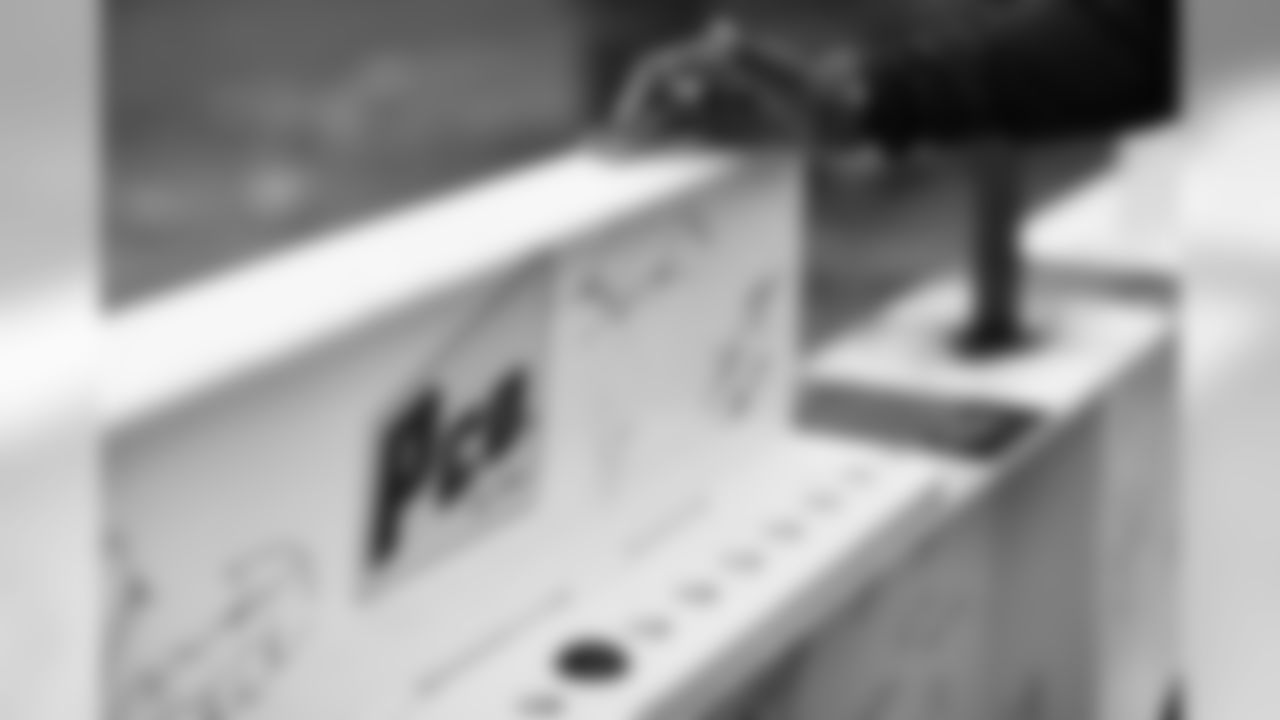
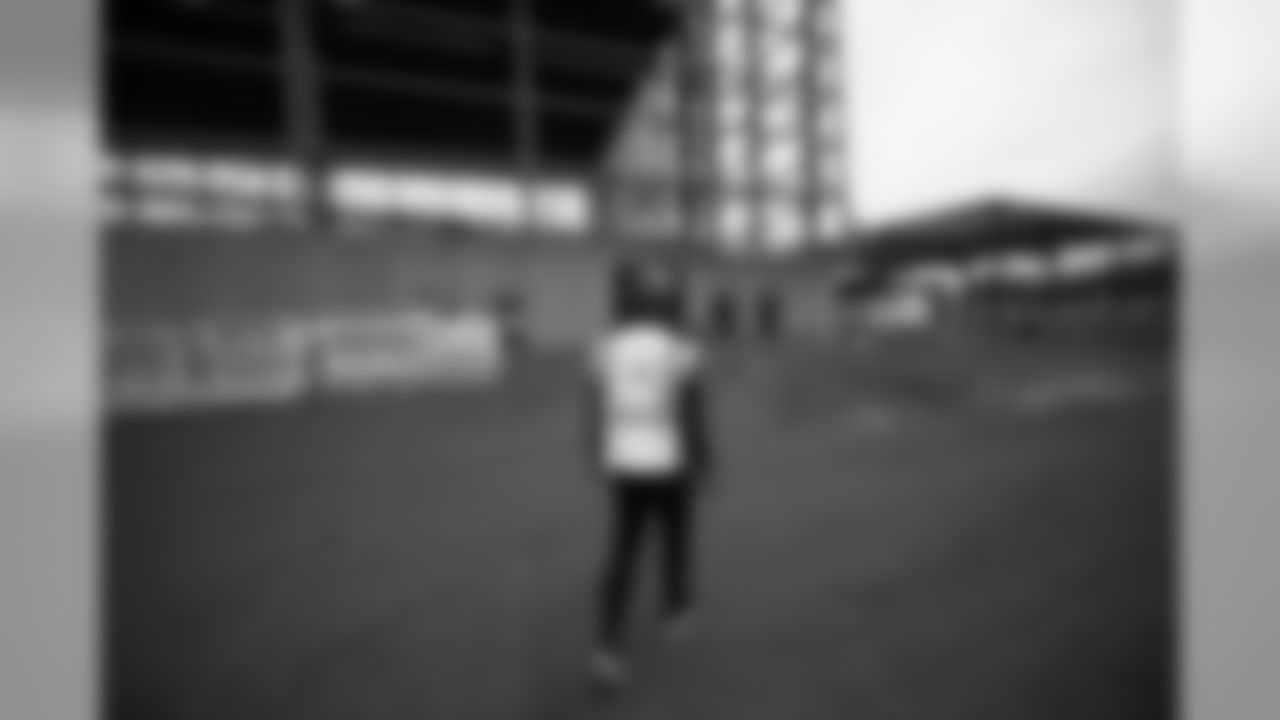
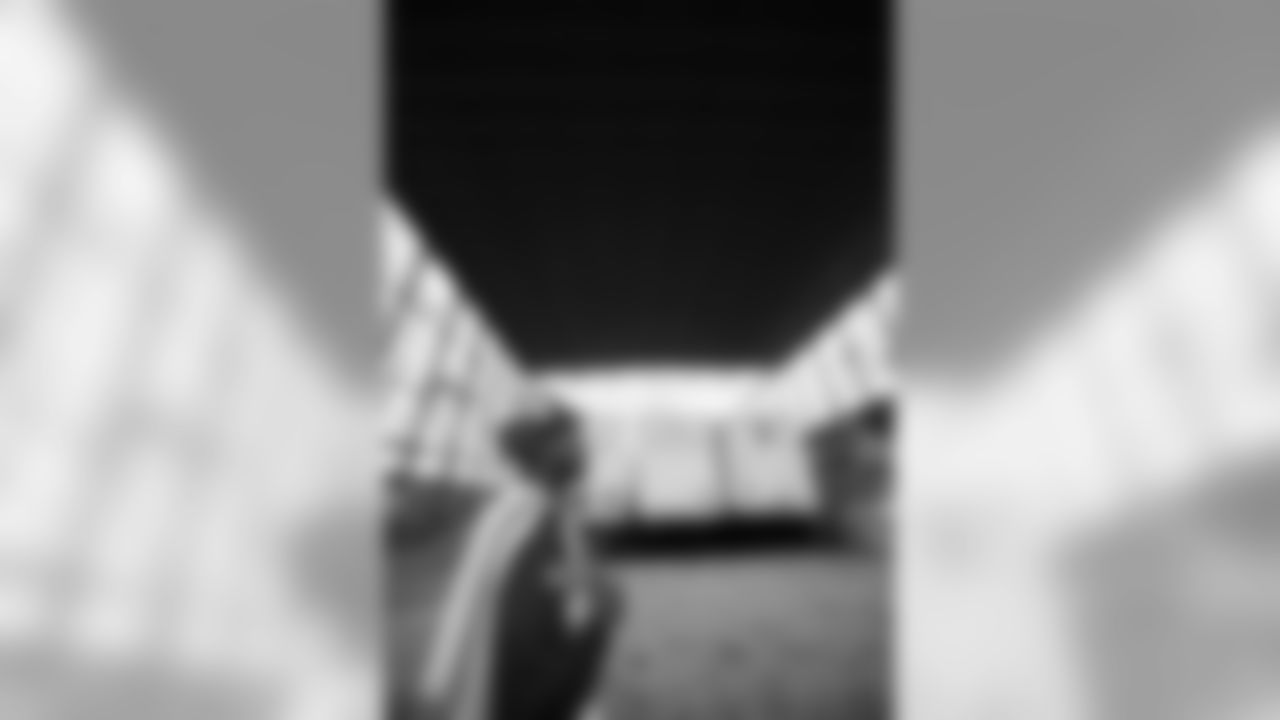
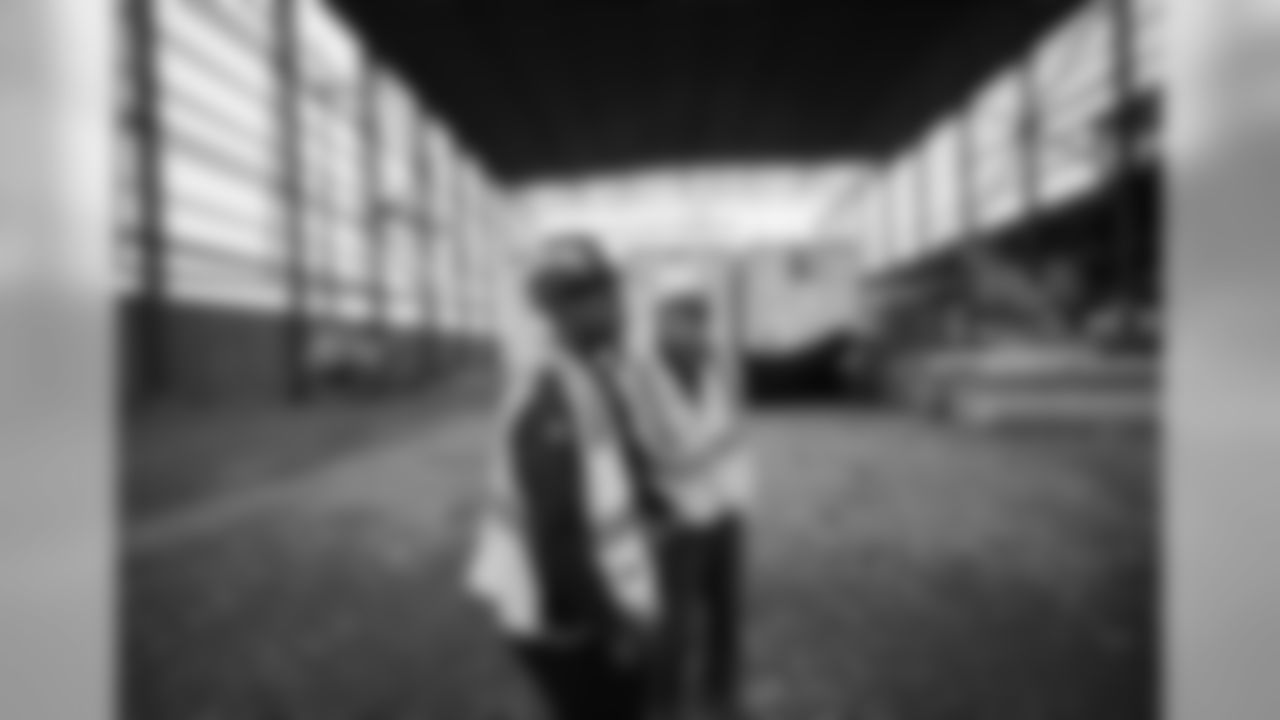
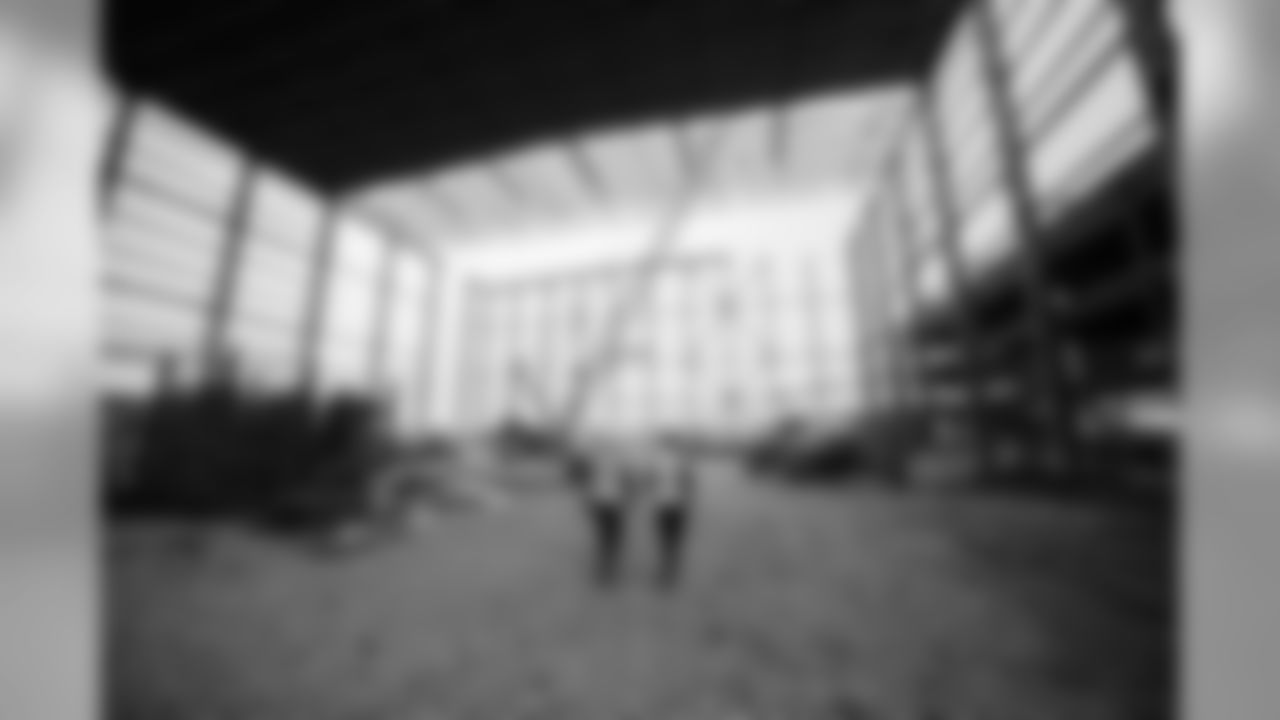
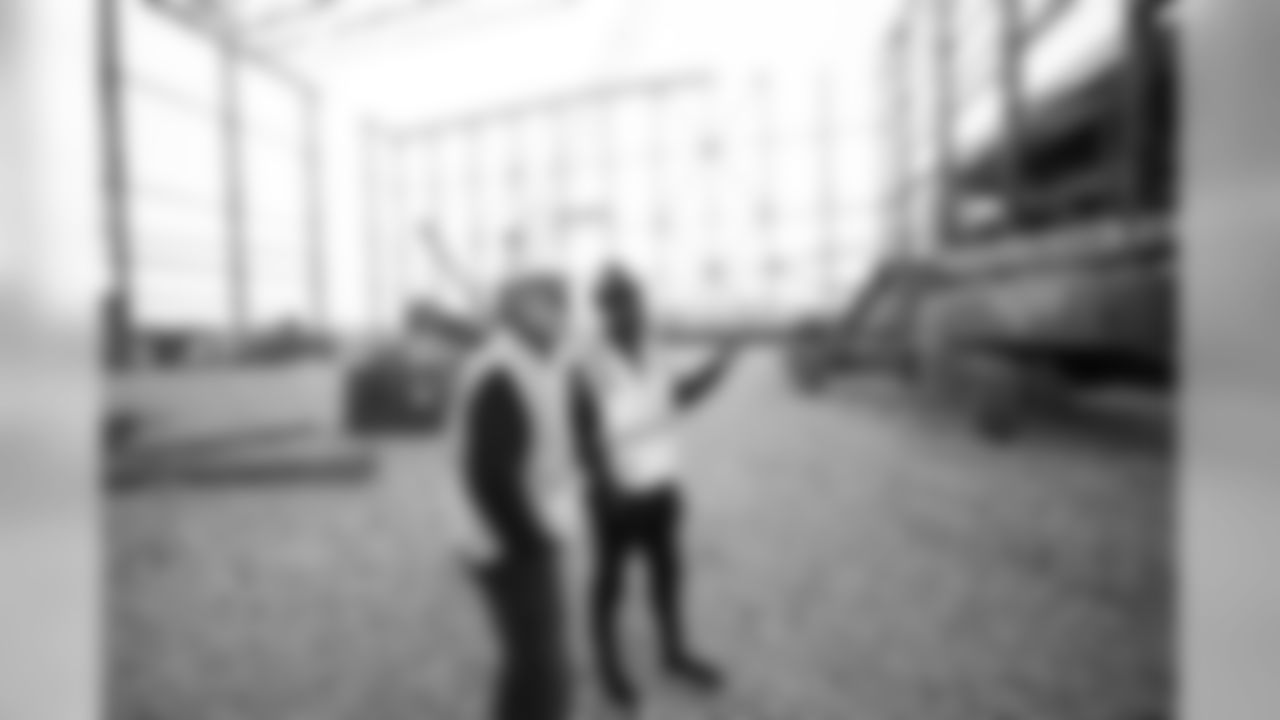
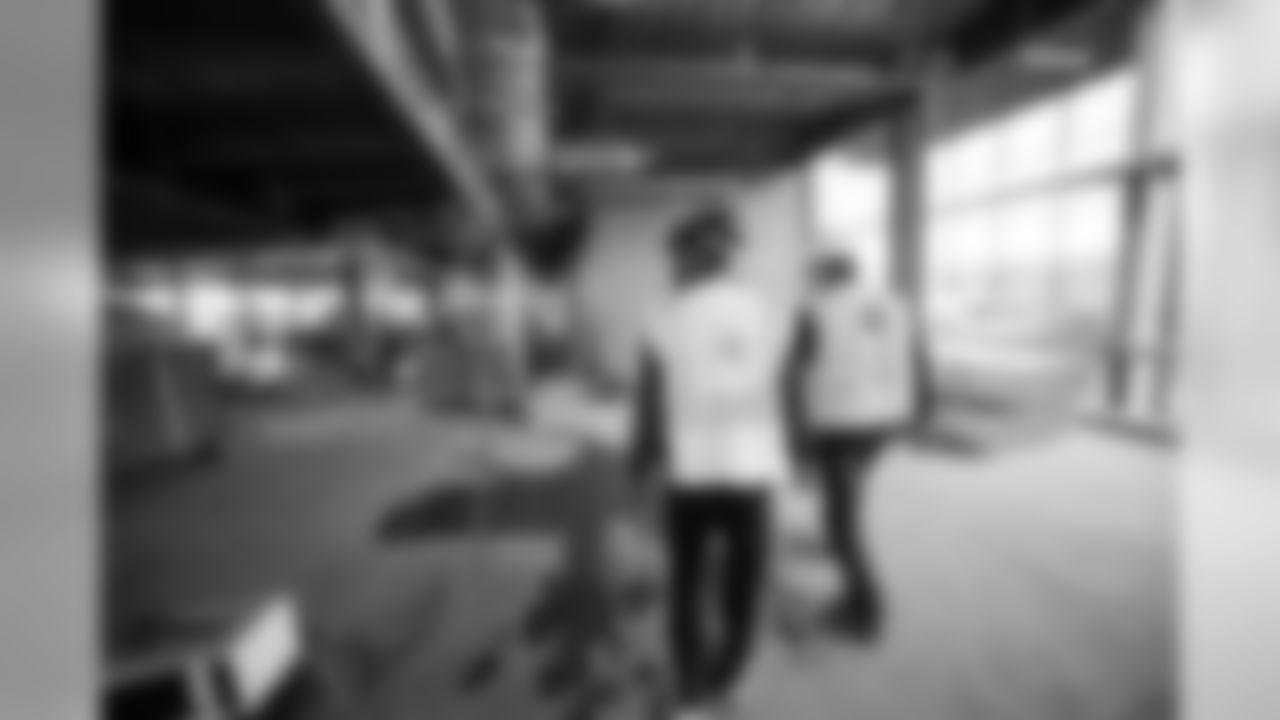
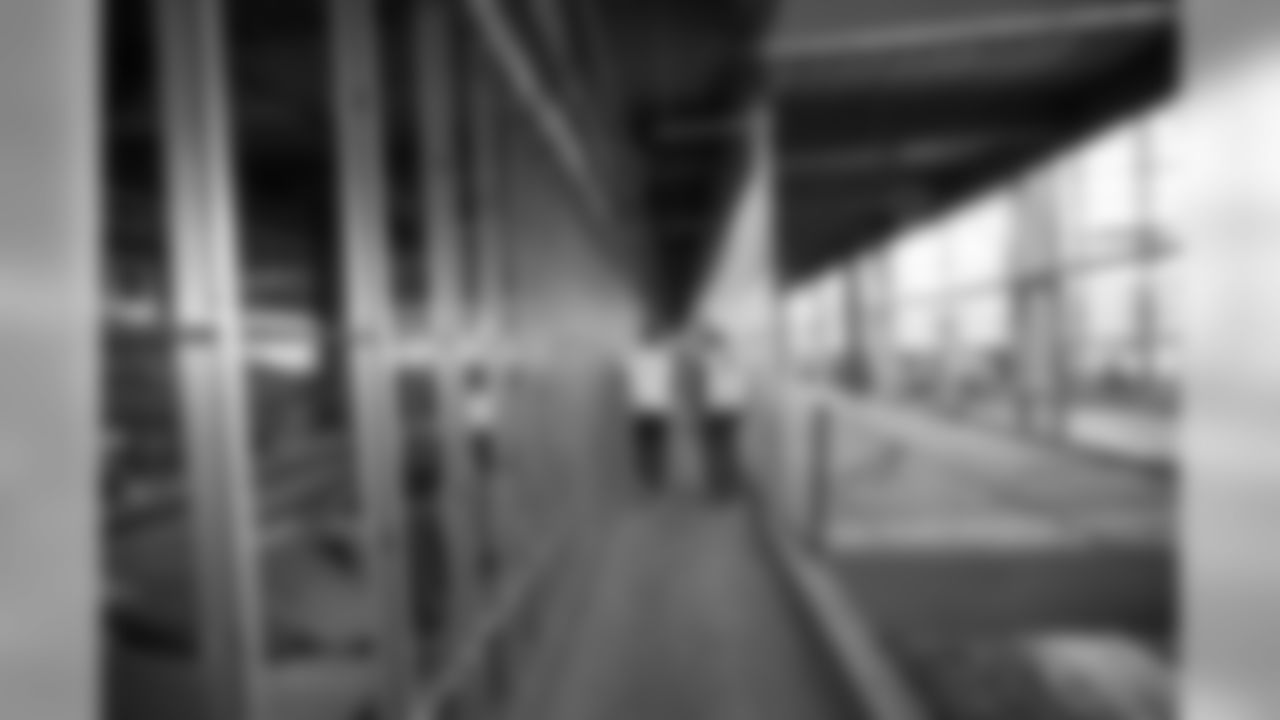
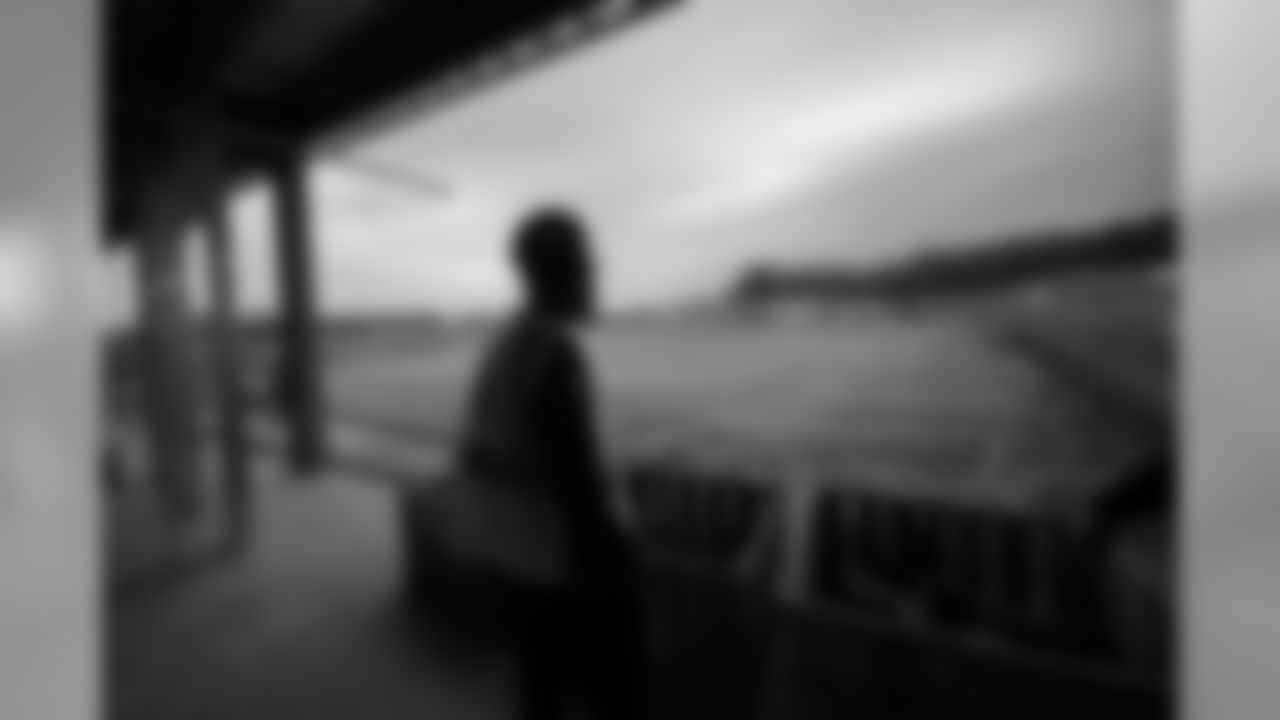
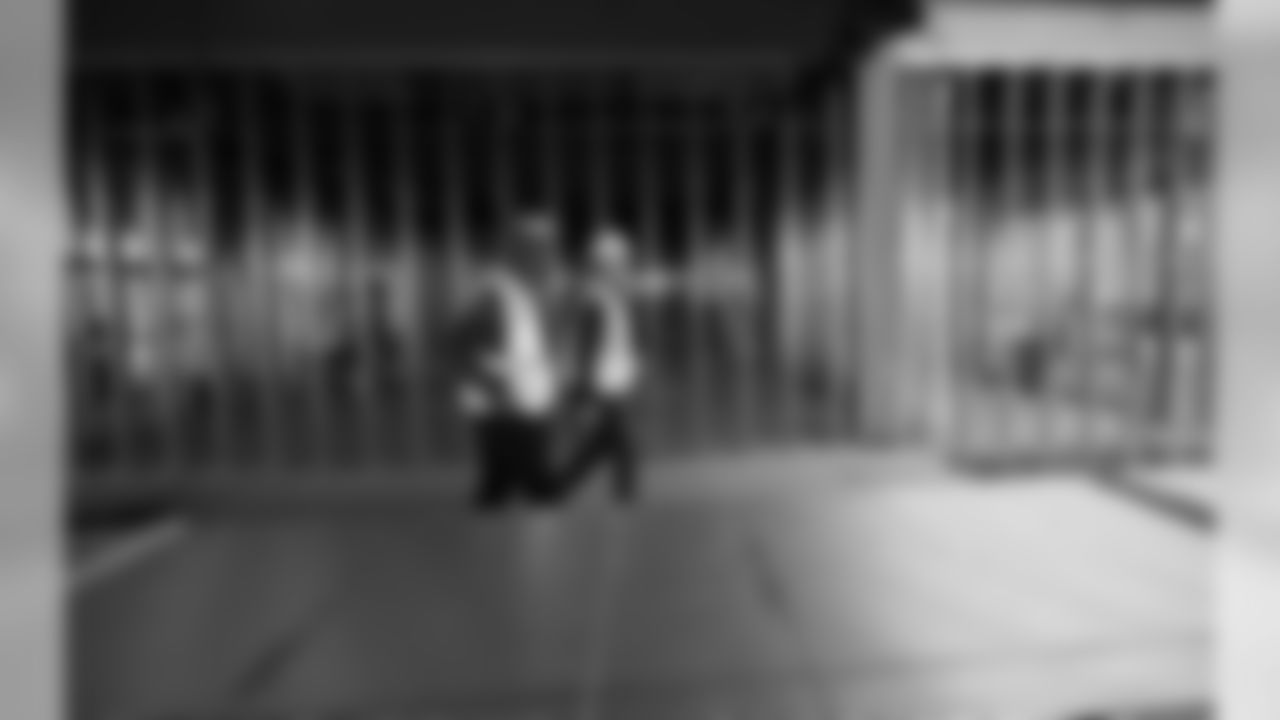
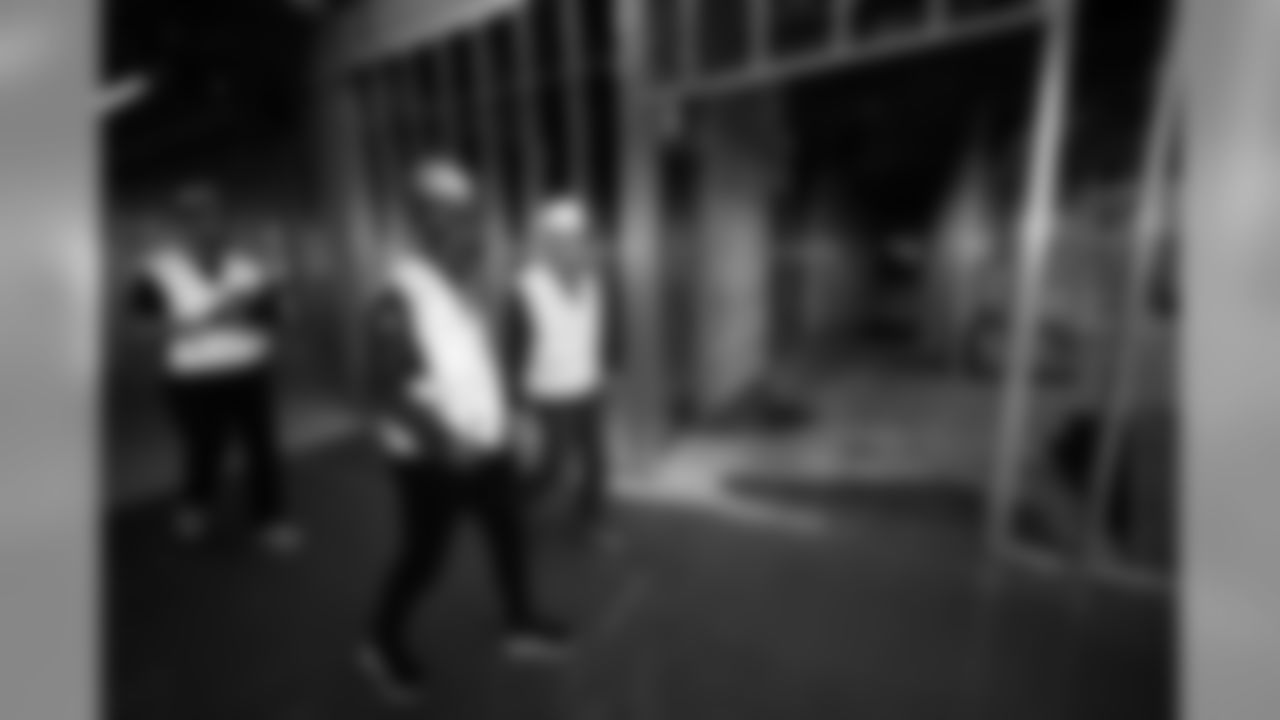
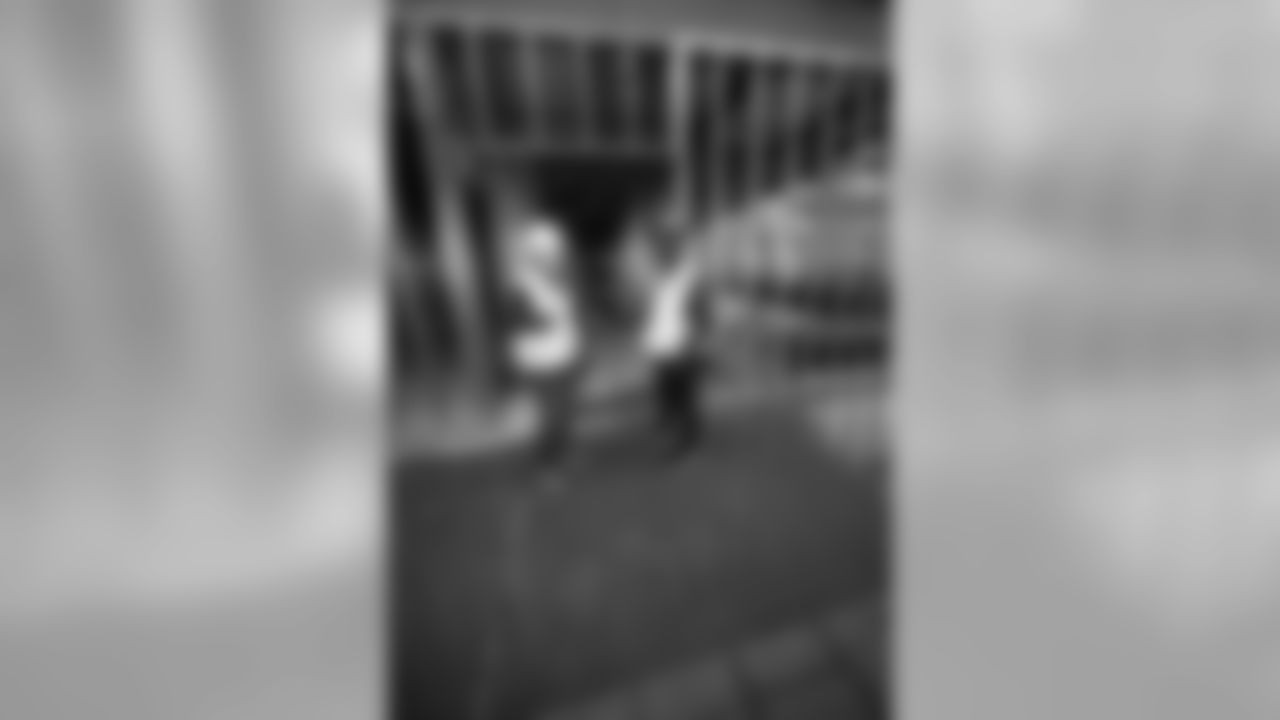
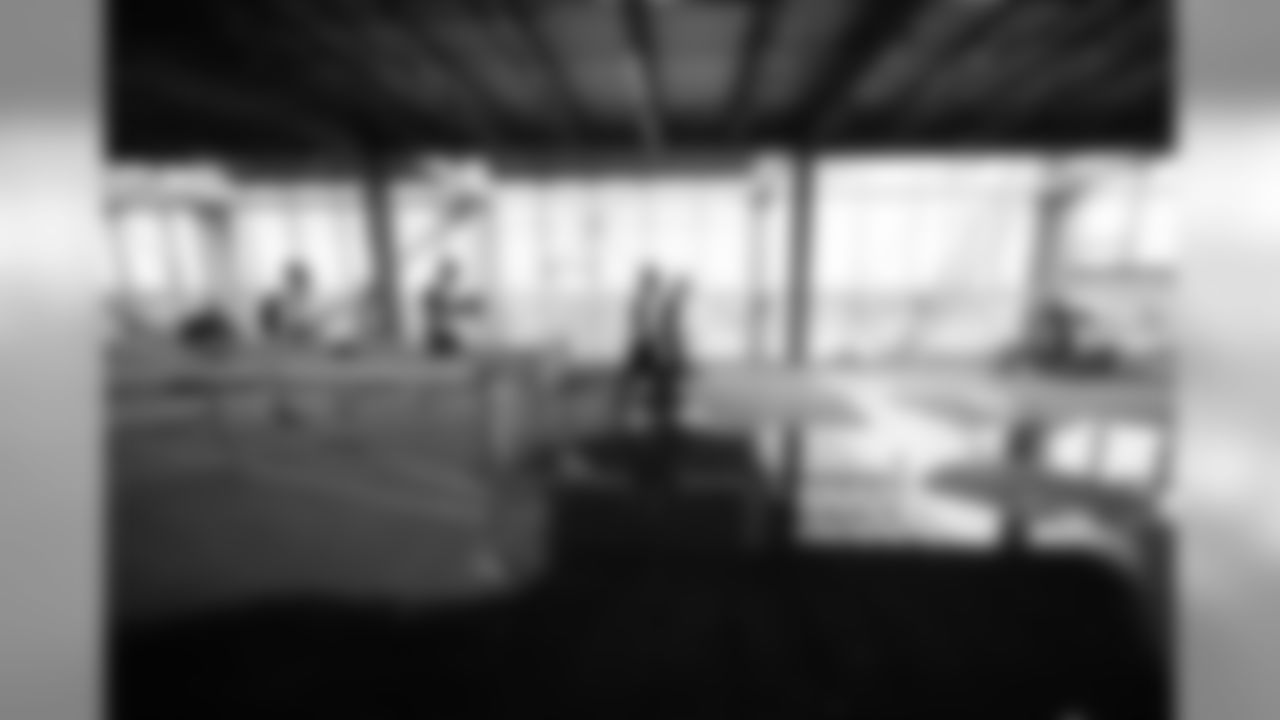
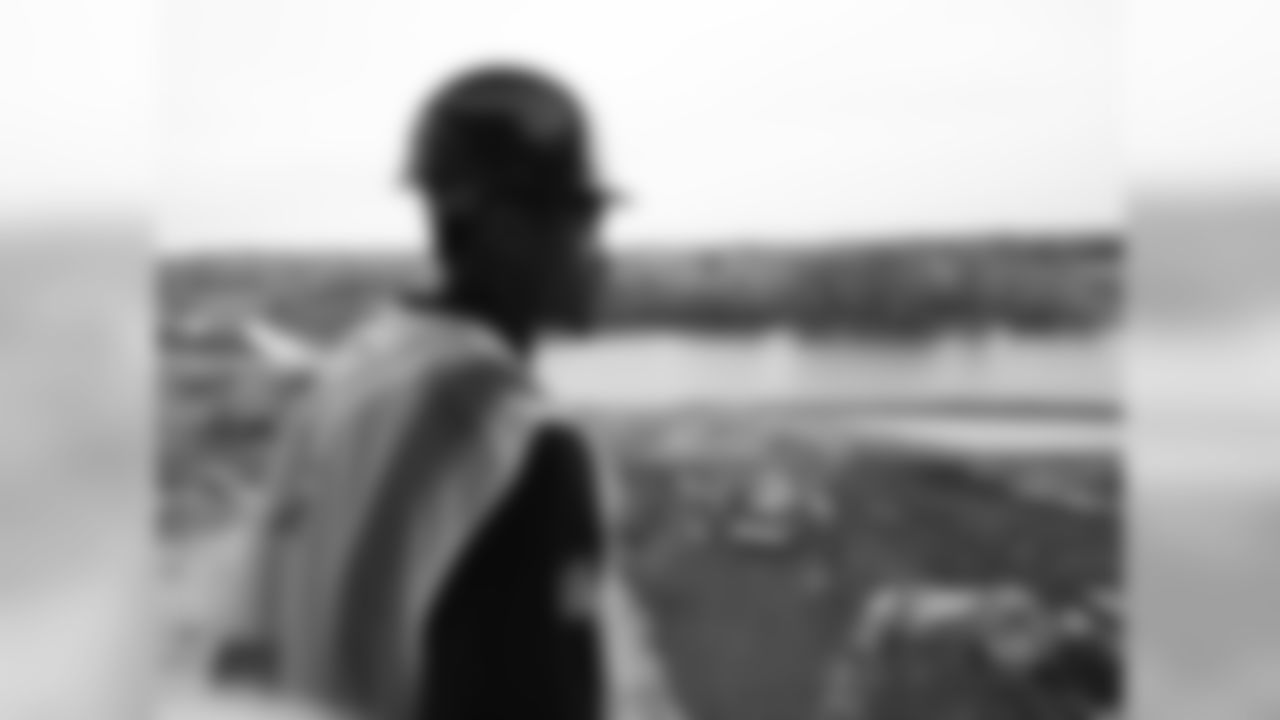
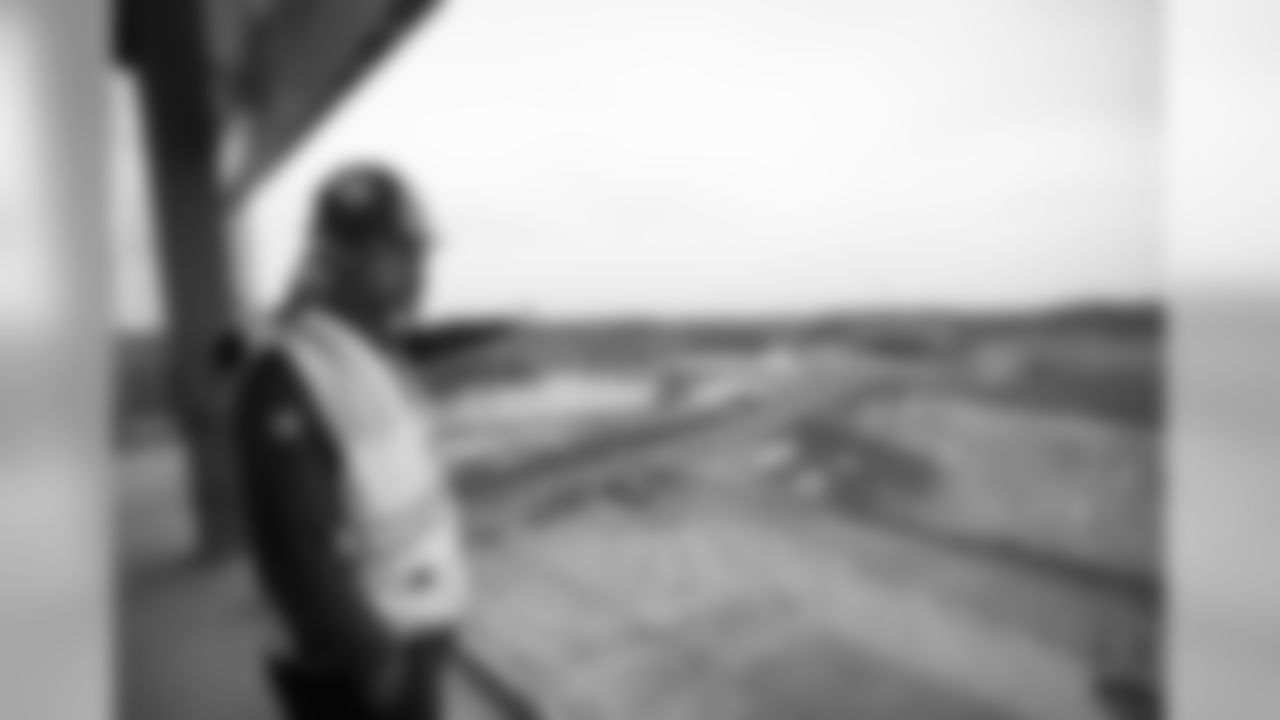
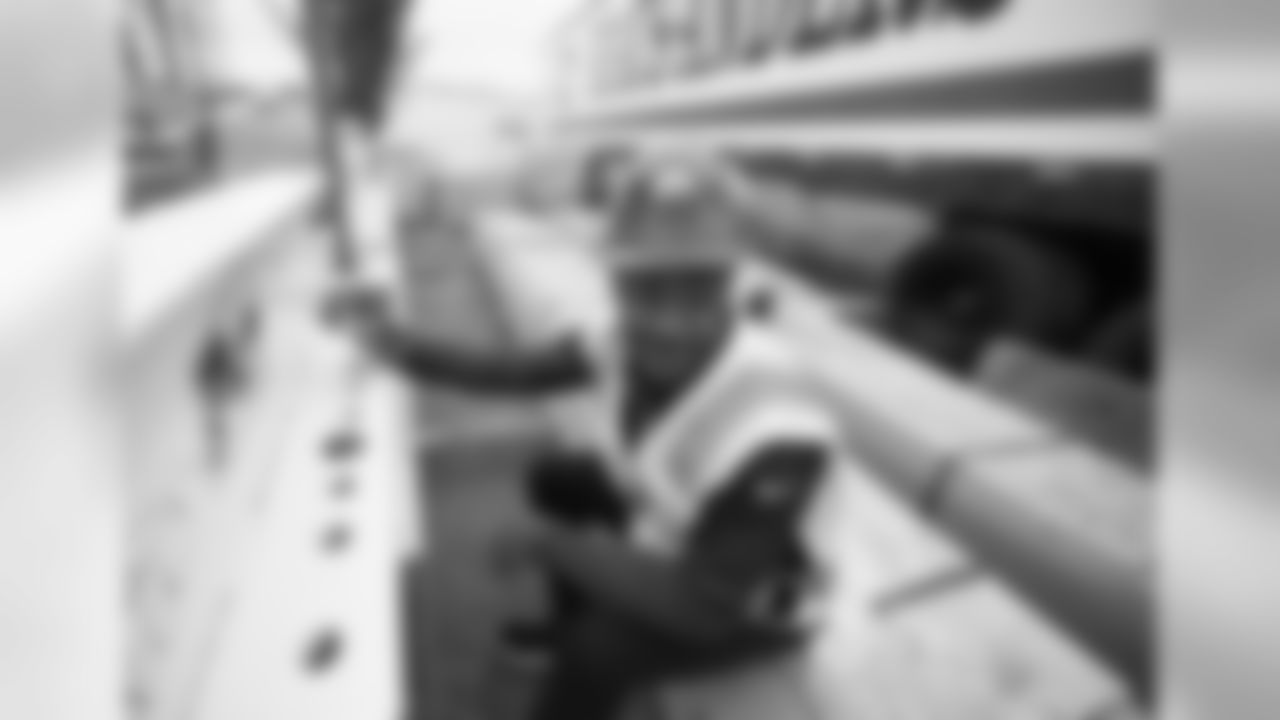
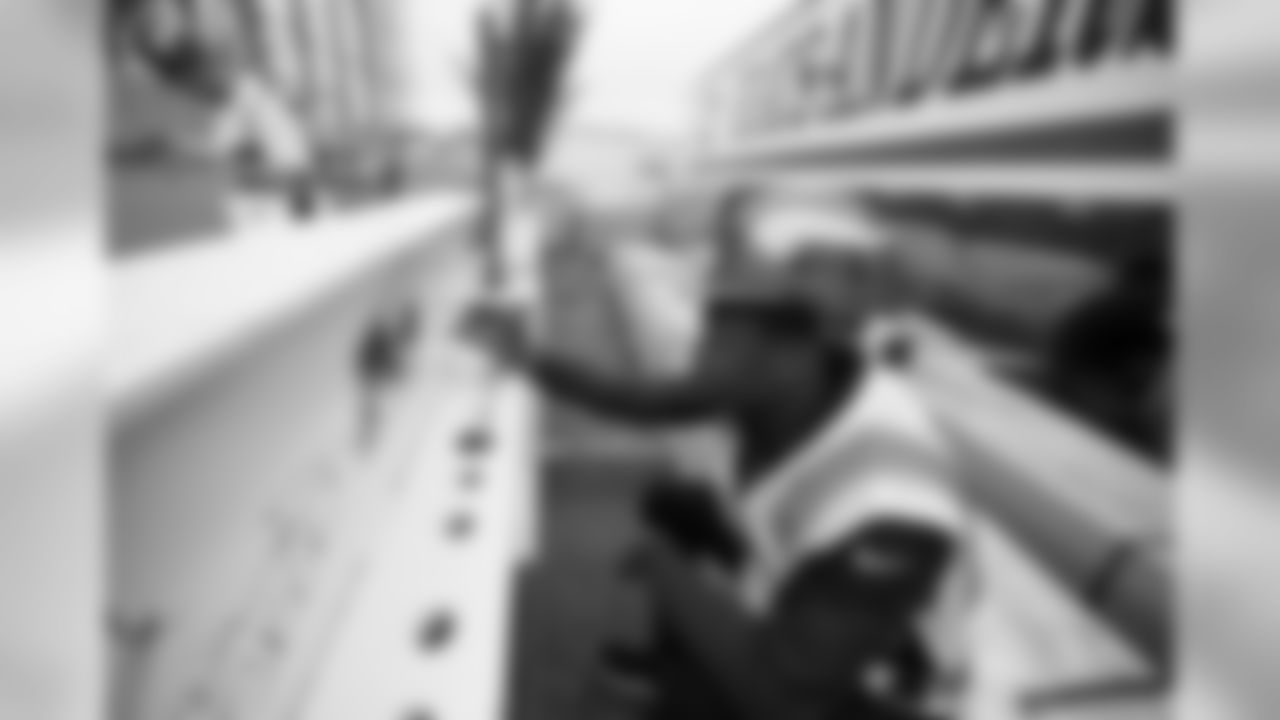
"You could just see in his eyes, walking around the IPF (Indoor Practice Facility), he's visualizing catching passes and running routes," Miller said. "That's kind of what we do as builders. We can see something on a piece of paper, and you have to visualize it in three dimensions in your head, break it down and put it in order with how it's going to get put together. That's one of the real excitements for me that I still enjoy after 33 years, trying to create real buildings from the designs."
Miller's construction roots began when he'd join his father, a plasterer, on jobs.
"I'd go to work with him in the summers and work with them on the weekends, cleaning, sweeping, just doing odd jobs, but I learned how to work, so that's been a really good trait," Miller said. "During college I had several jobs to get through college. When I started, I kind of knew what I wanted to do, I fell right into it, and I've been doing it ever since."
Miller, a Kansas native who grew up in California, graduated from Cal Poly Pomona and worked in Los Angeles for 10 years. During that time, he roomed with a co-worker in the Long Beach neighborhood of Belmont Shore.
"A nice young lady" moved in next door when she transferred from Minnesota, and Miller happily helped his future wife, Anne, adjust to new surroundings.
"She didn't have a clue of where things were or why things were so expensive," Miller said.
Miller has gone from high-rises in Los Angeles to high-profile projects in Minnesota, where he's lived and worked for the past 23 years.
"Certainly to be able to work on this project with the Vikings, the most-recognized name and logo in Minnesota across the country, is really exciting," Miller said. "The last big job I worked on was at 3M, so I've had the great fortune of working on high-profile projects. I kind of like that.
"I did a lot of high-rises in downtown L.A., and those are still some of my favorites," Miller added. "Any time you get a backdrop of downtown L.A. and see the three tallest buildings, I was able to work on those and had some part in their construction."
In addition to working on the First Interstate, Deloitte, ARCO and Biltmore towers on the West Coast, Miller also worked on the Federal Reserve Bank in Minneapolis.
"That was my first job here in the cities," Miller said. "That was really cool, had a lot of different things, just like the TCO Performance Center does. You do not have many opportunities to build a robotic cash vault or check-processing center or ballistic-rated walls."
The uniqueness of TCO Performance Center, from hydrotherapy pools and a cryotherapy chamber to a large locker room with two fireplaces and custom-designed lockers to team meeting spaces, a cafeteria, indoor practice facility, four outdoor fields and TCO Stadium has presented opportunities and challenges. Those are joined by the needs to stay on schedule and budget while smoothly incorporating changes.
"There are several items in here that I'll probably only be able to work on one time," Miller said. "We don't know everything, but we have been exposed to a lot of things over the years. I tell our guys, use your same core principles to gain knowledge and understand the specifications and drawings. That helps to make sure vendors and subcontractors are supplying what is called for and get it installed right the first time."
Miller, who now lives in Mendota Heights, said building relationships with clients during construction projects is an important part of the process.
"People are interesting to work for. We try to learn and put ourselves in the clients' shoes and say, 'What's going to be important to the clients?' and 'How are they going to use the building?' We try to learn as much as we can to be as helpful as we can be so it's not just a transaction."