PLYMOUTH, Minn. — Jim Malecha can remember — albeit with a smile — attending Vikings games at Metropolitan Stadium in snowmobile suits.
Like many who became lifelong supporters during the Purple People Eaters era, the Faribault native attended the last game at the Bloomington venue that was replaced by Mall of America. The temperature at kickoff of the final game was 21 degrees Fahrenheit, further enhanced by a 16-mph southeast wind.
Snowmobile suits were no longer needed once the Metrodome opened in downtown Minneapolis in 1982, but external views were sacrificed behind the opaque walls.
See how Minnesota-based InterClad is working with the latest technology to make sure the gameday experience is a comfortable one for fans at the new stadium.
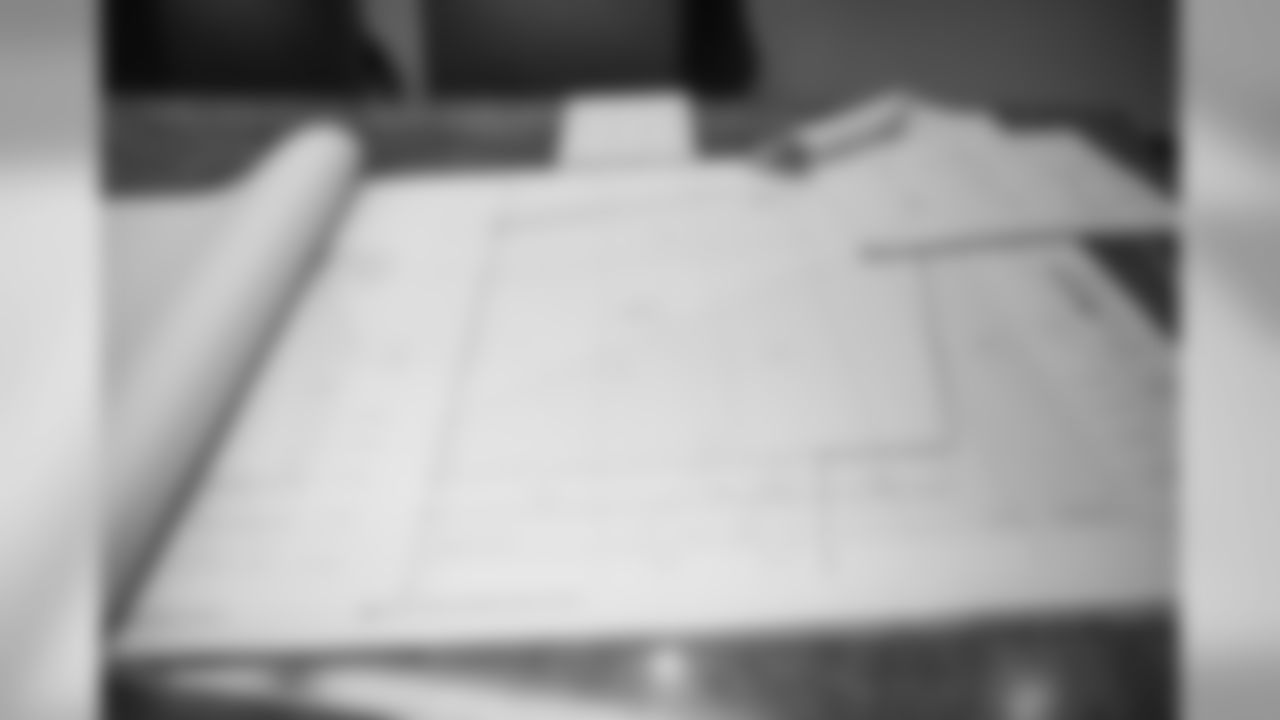
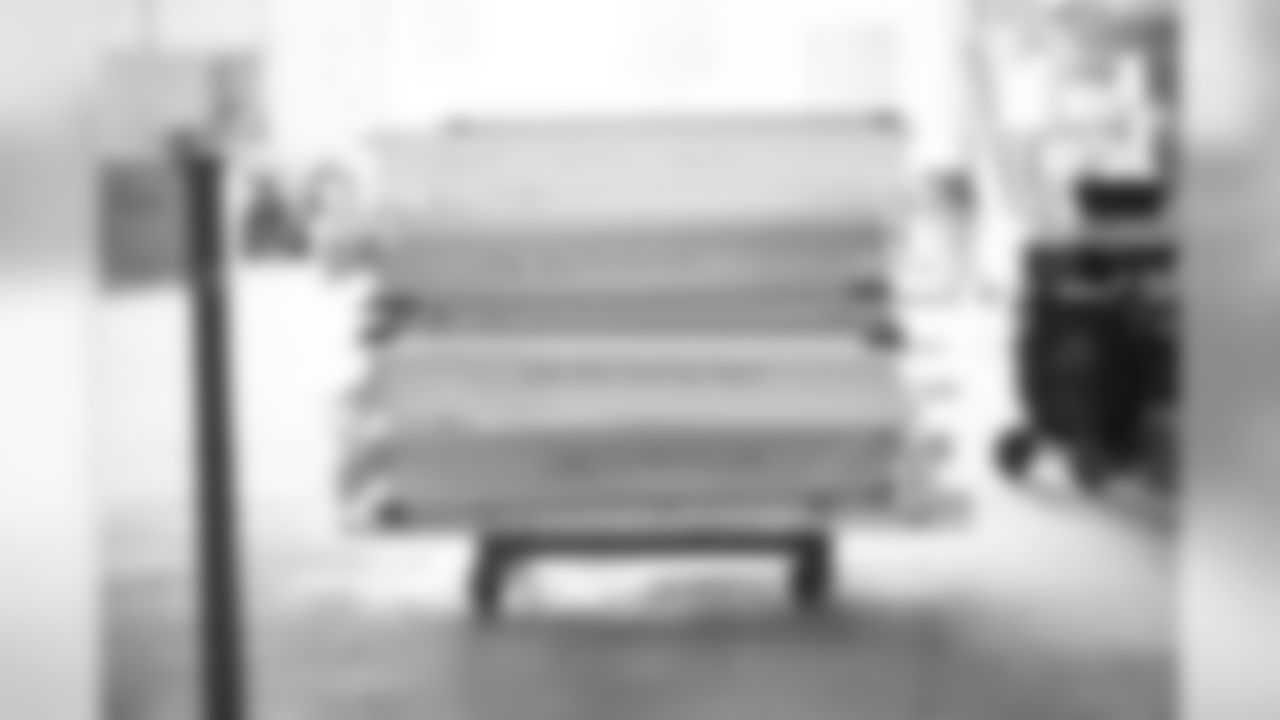
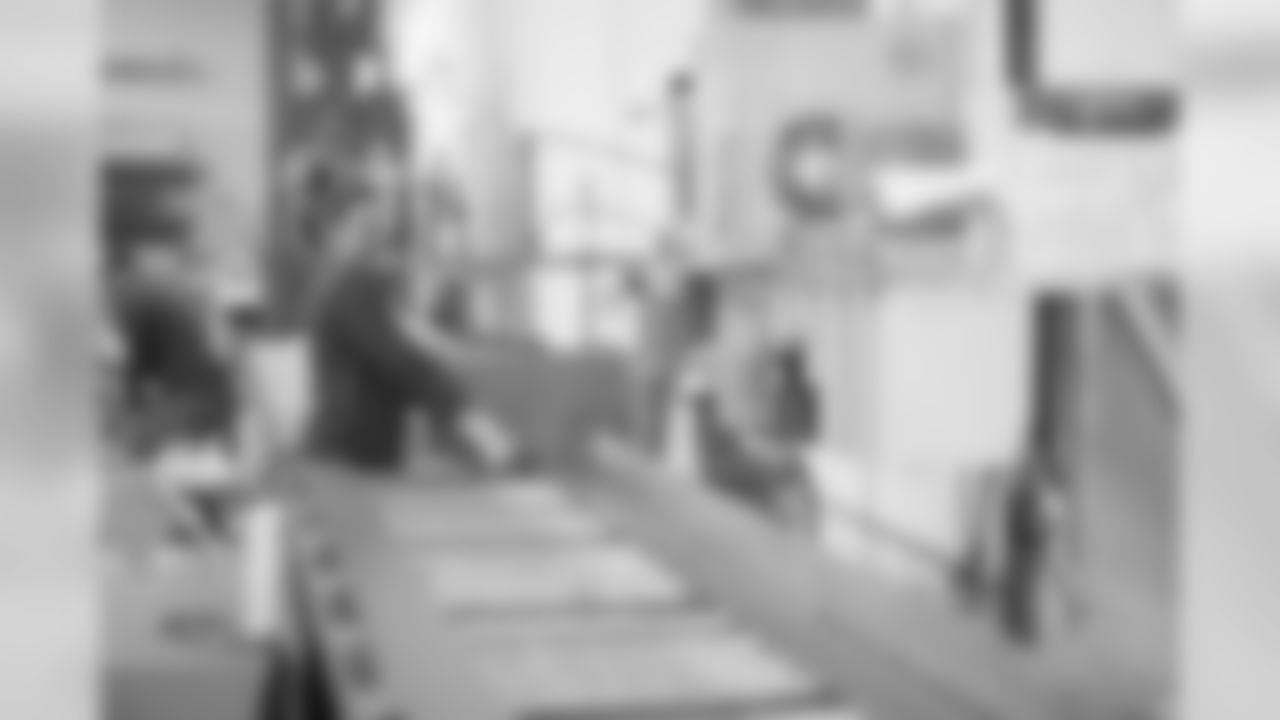
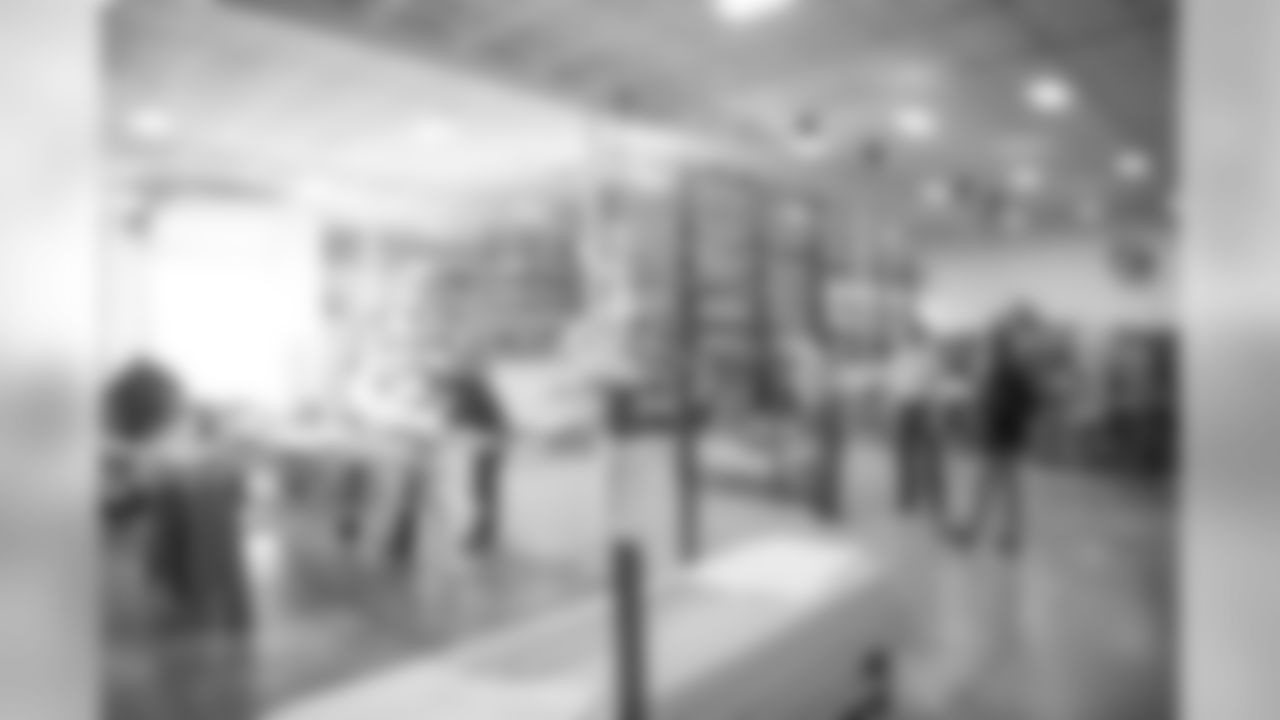
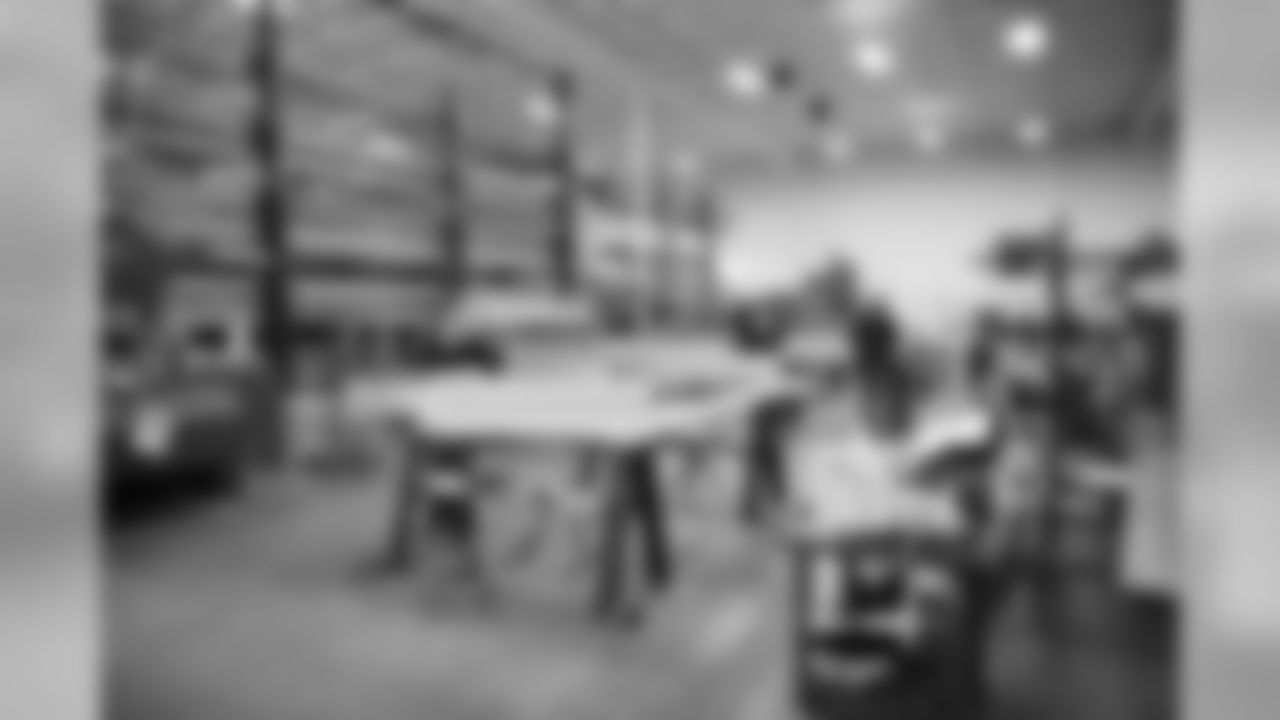
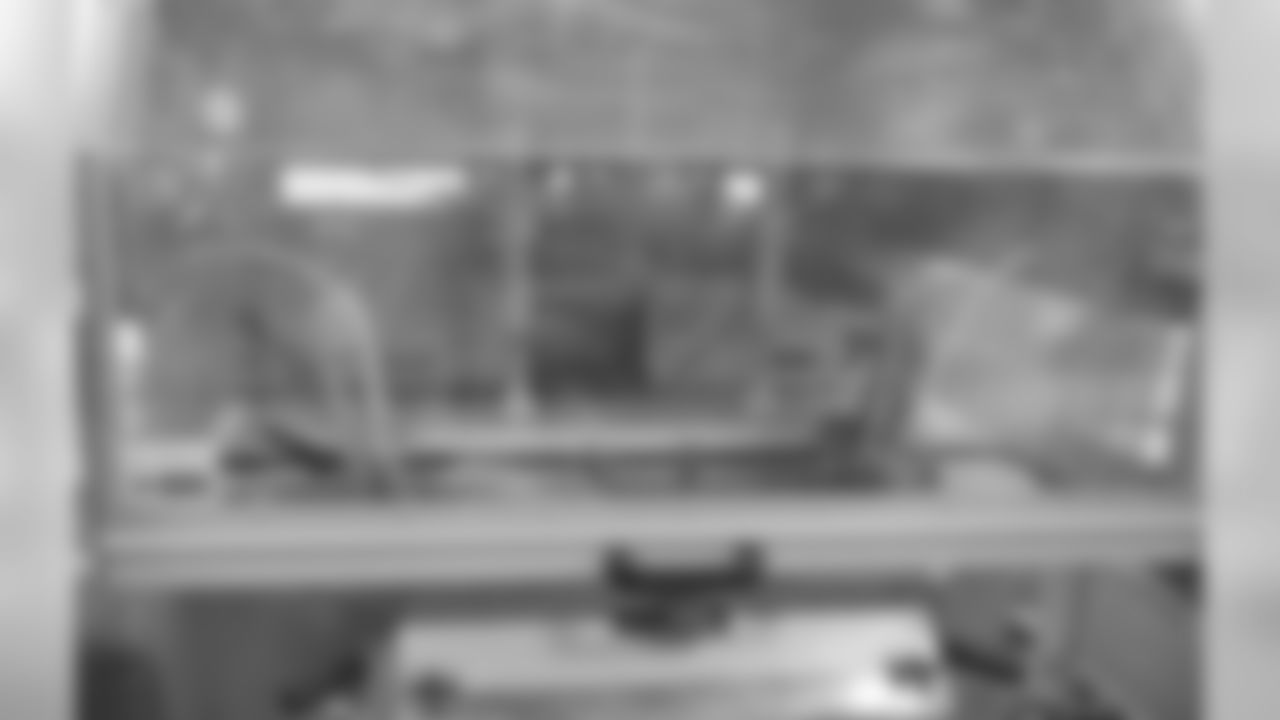
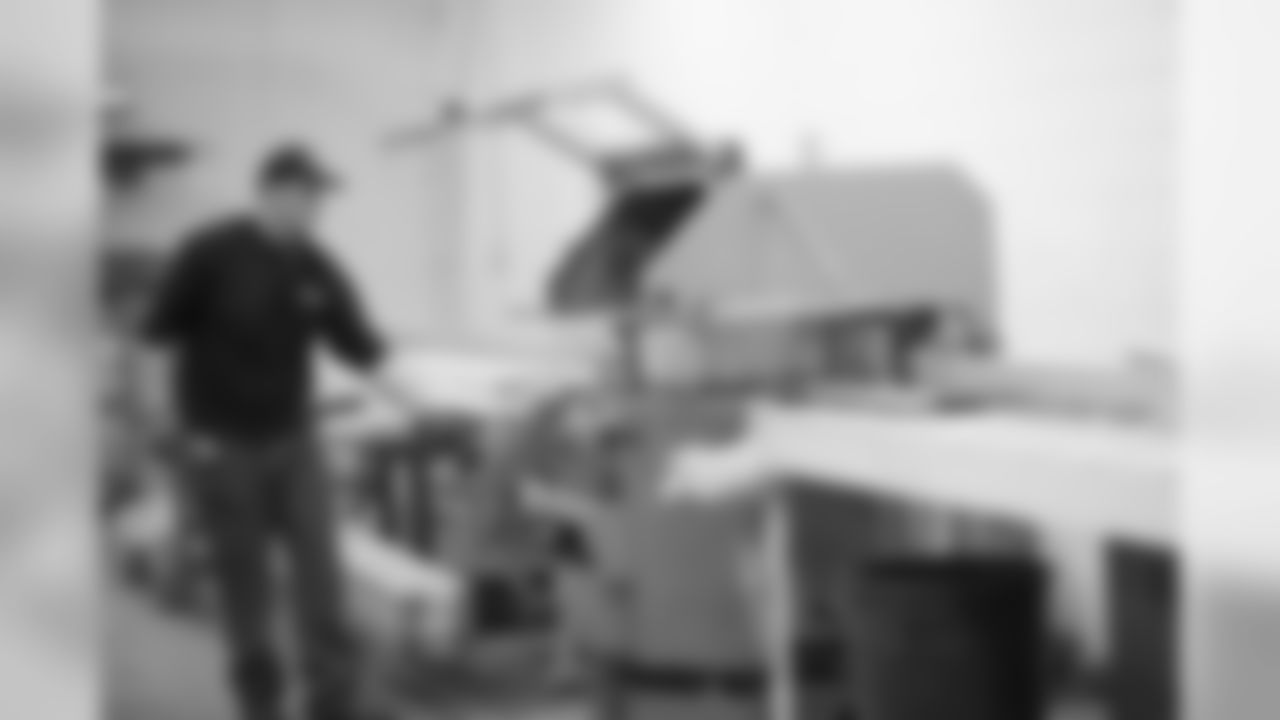
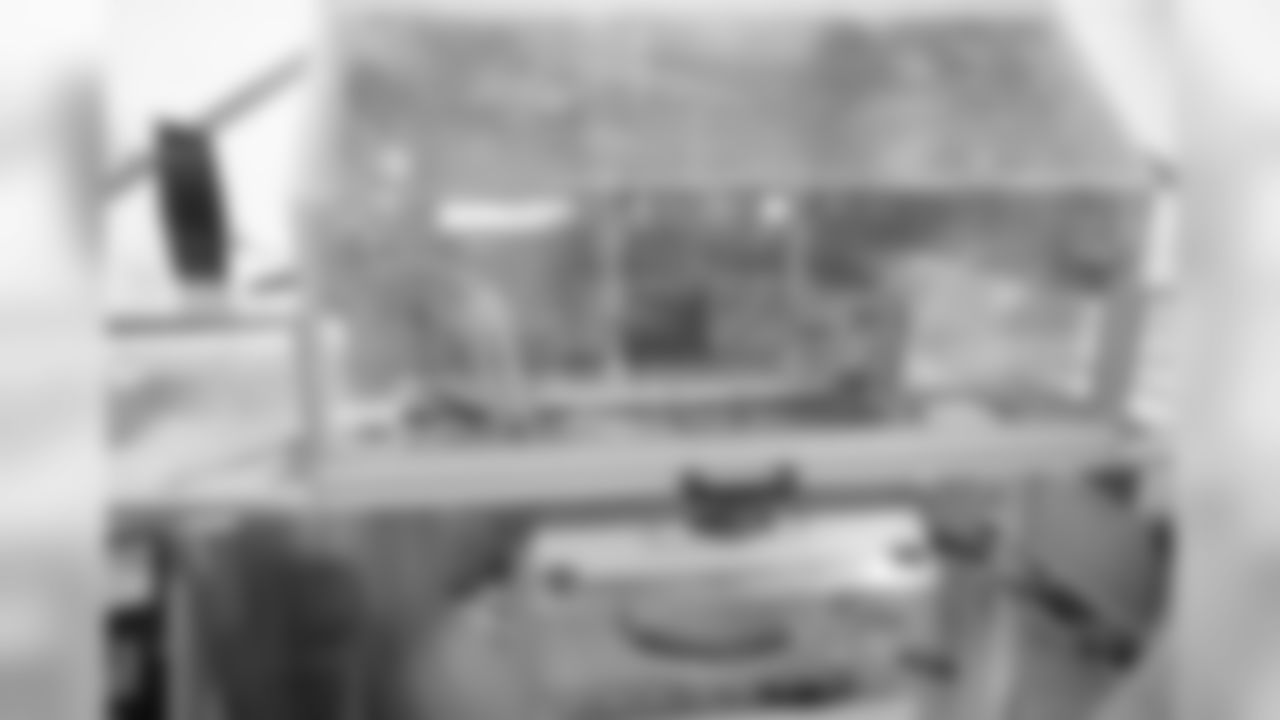
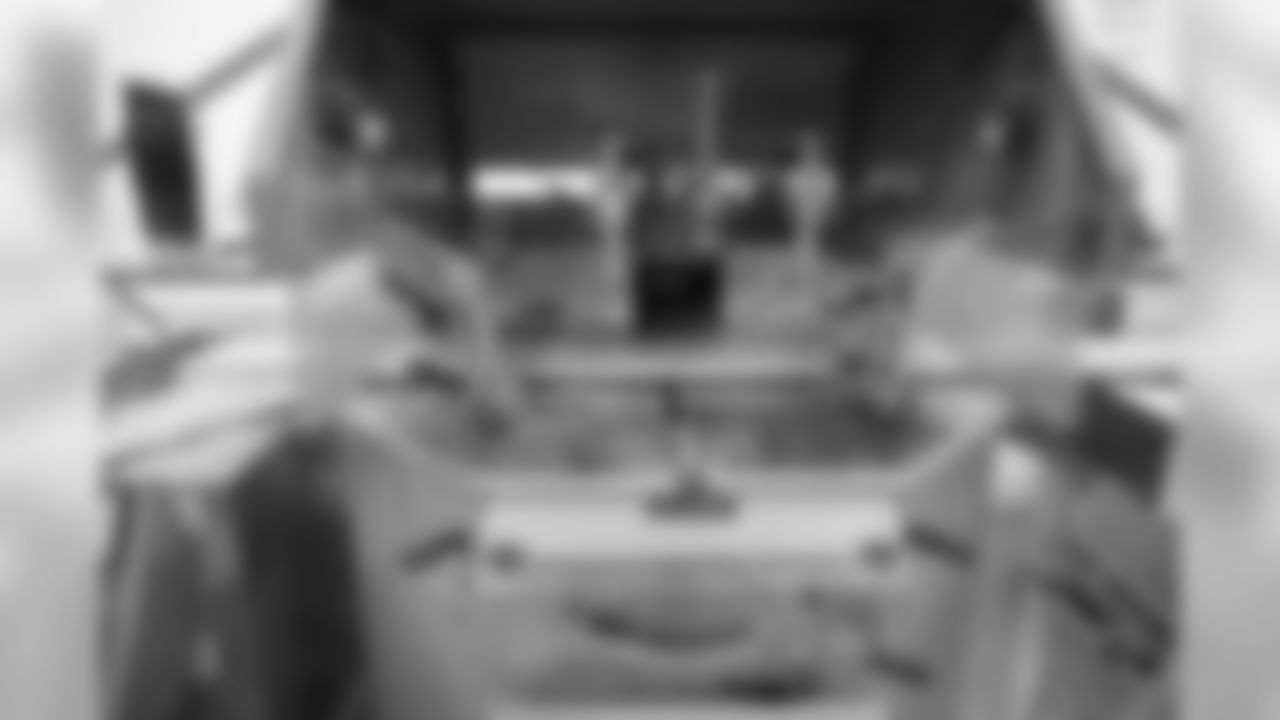
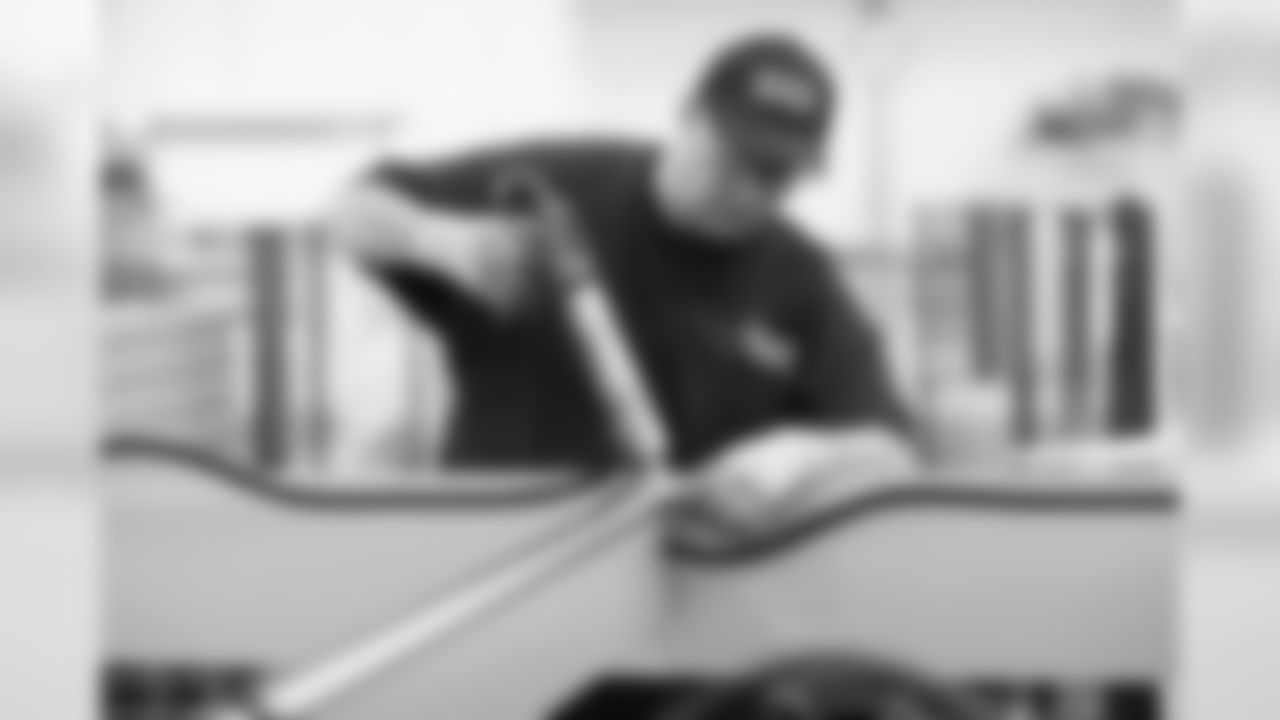
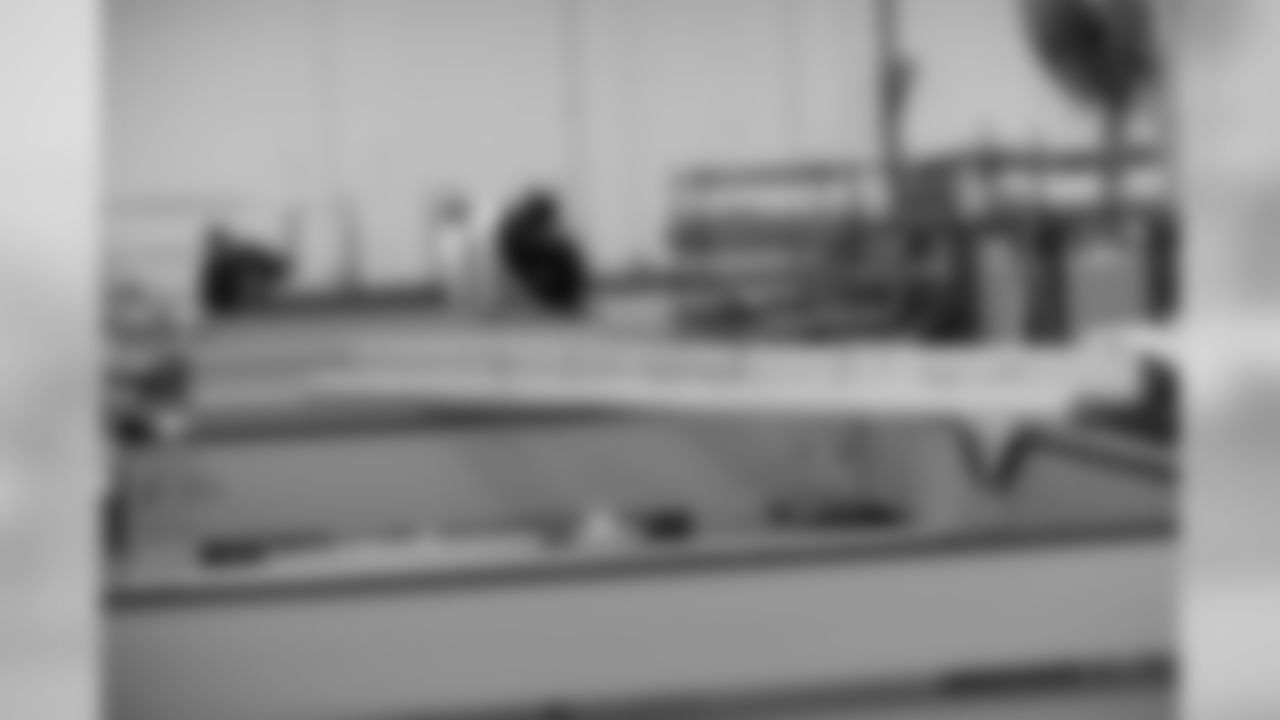
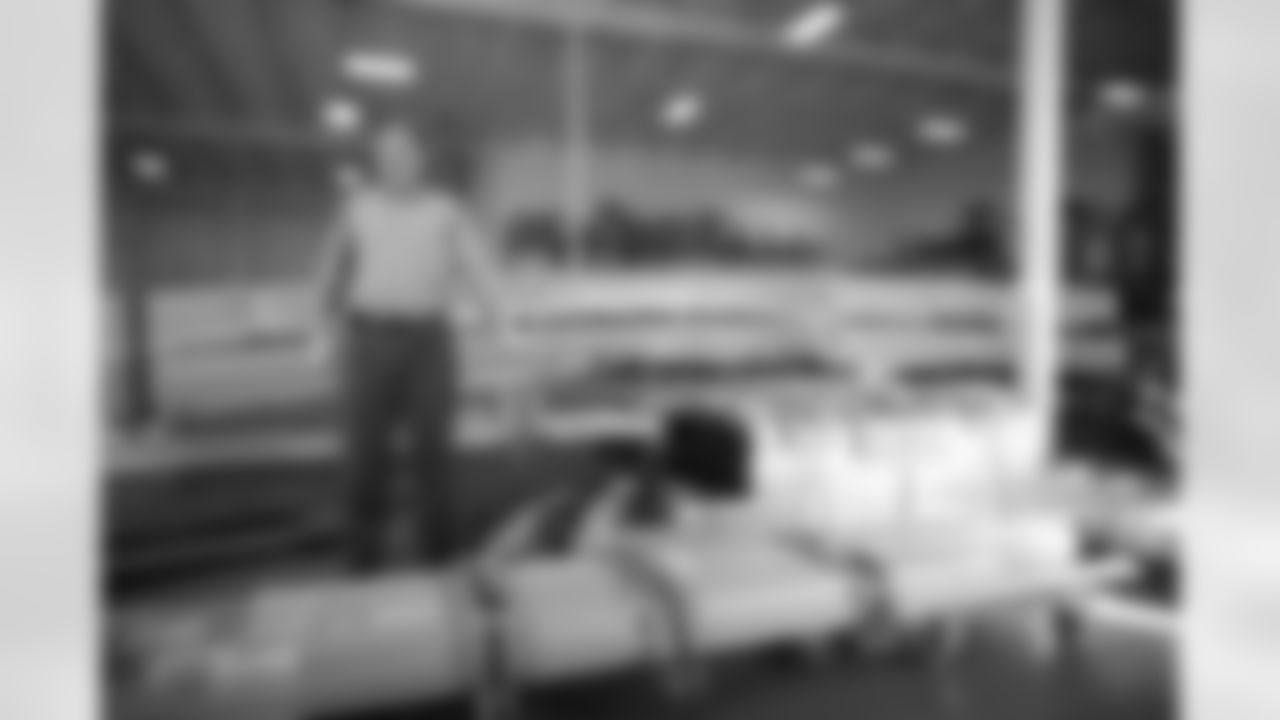
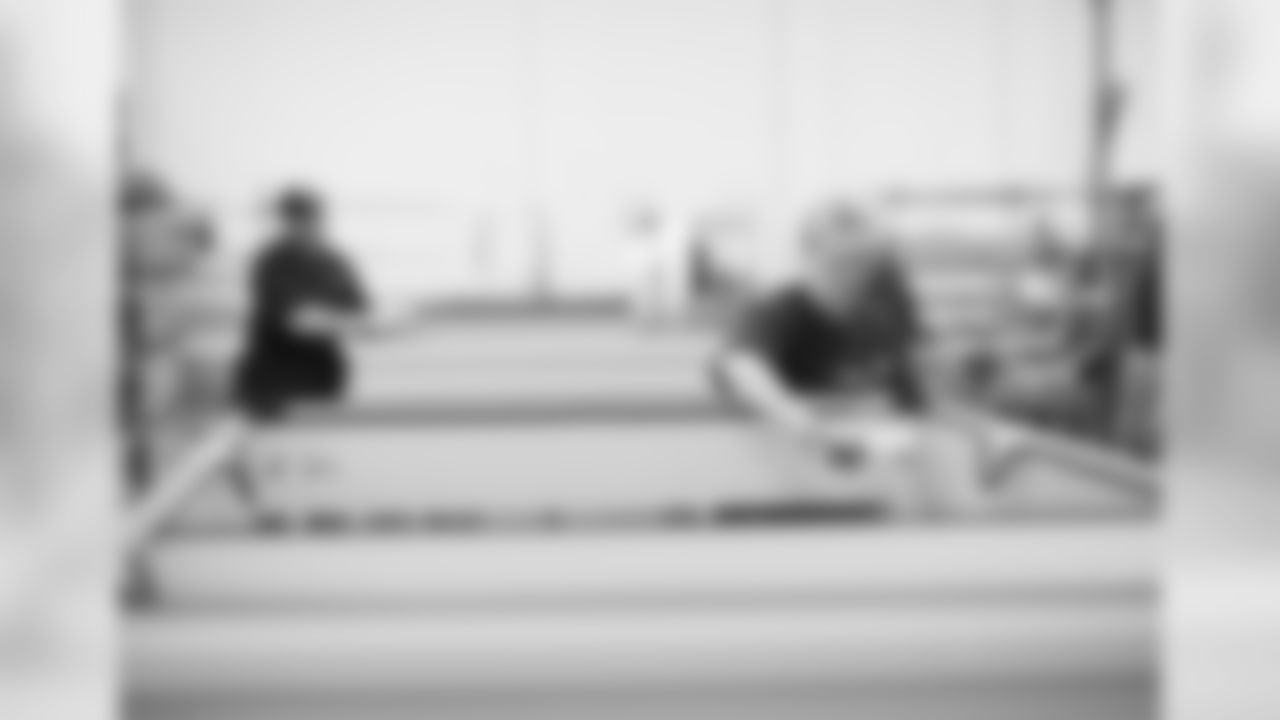
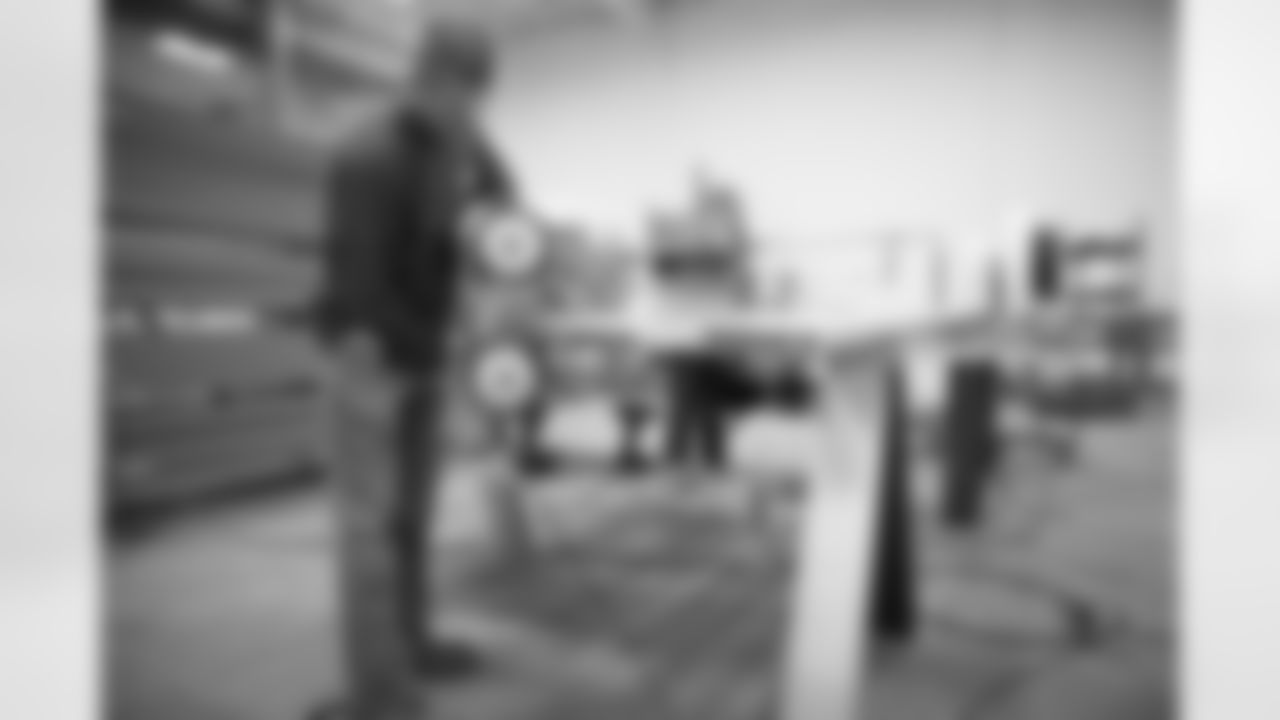
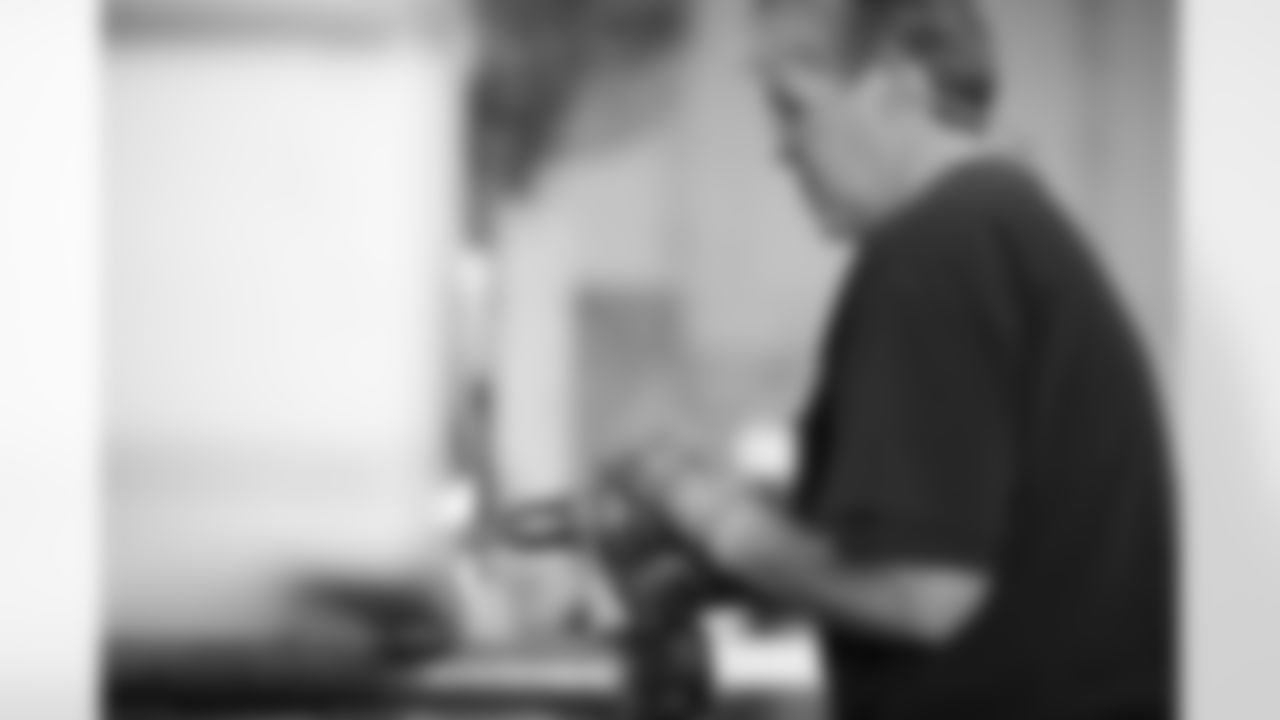
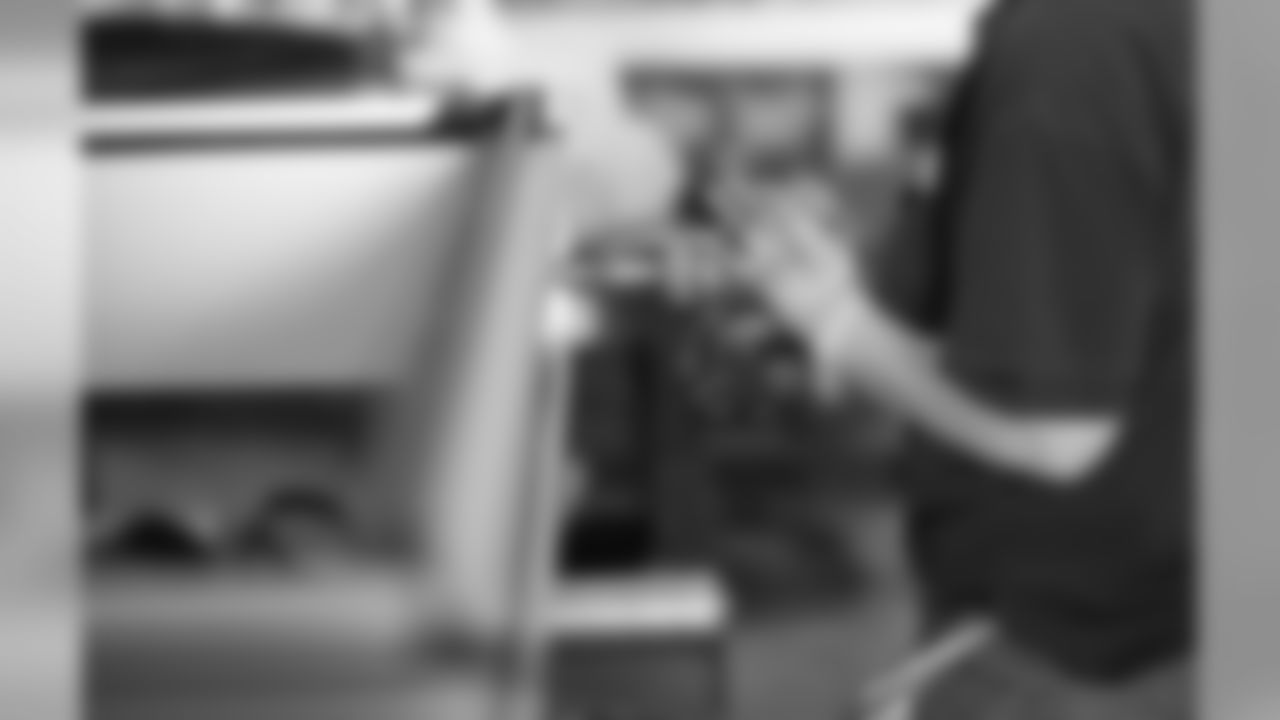
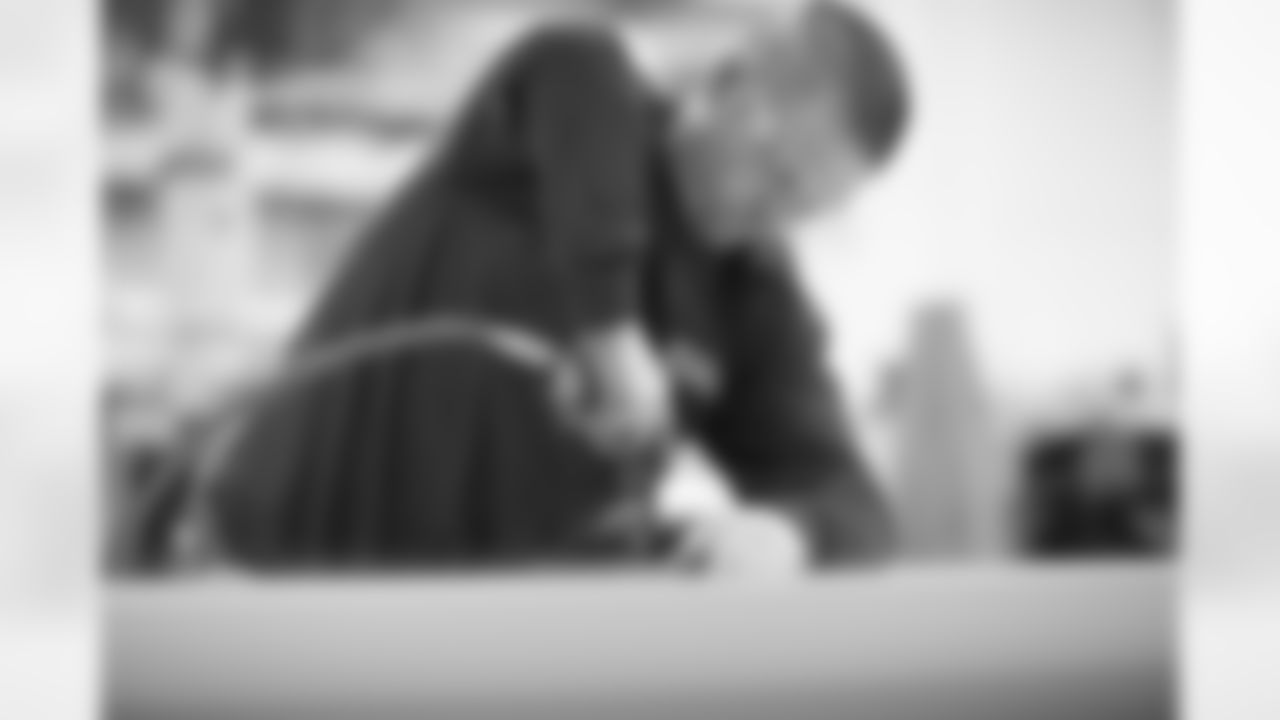
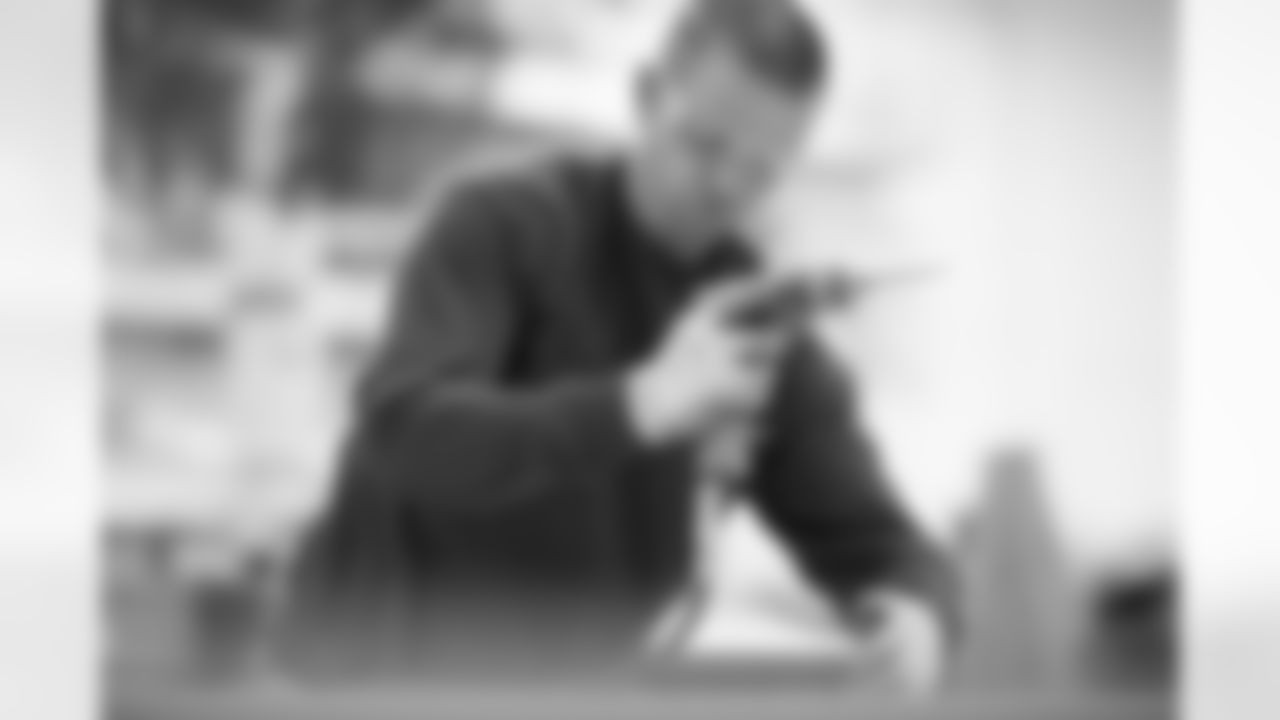
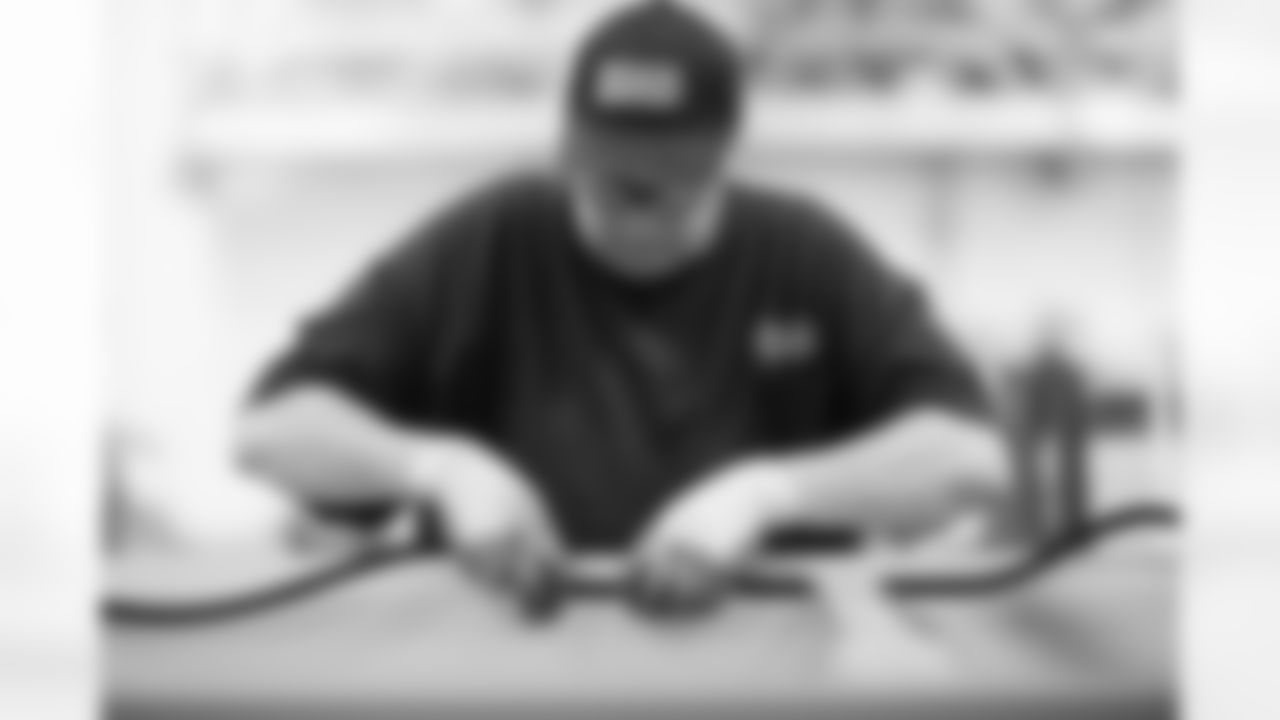
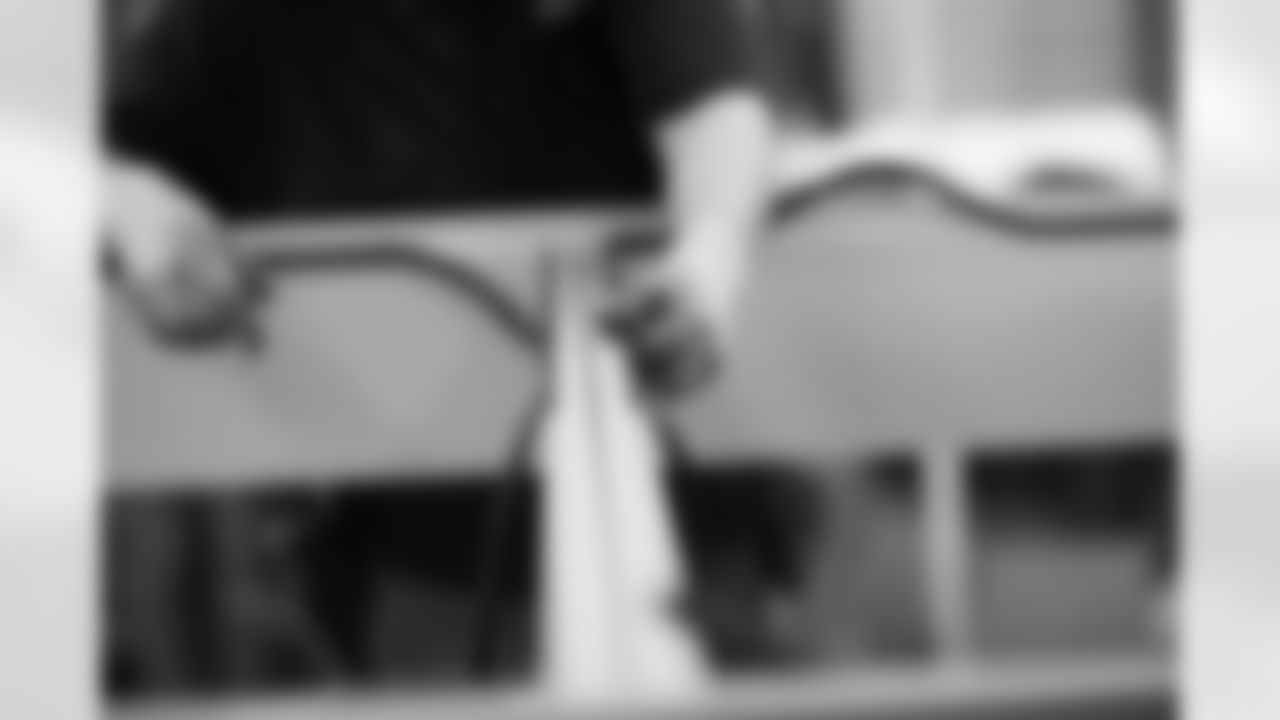
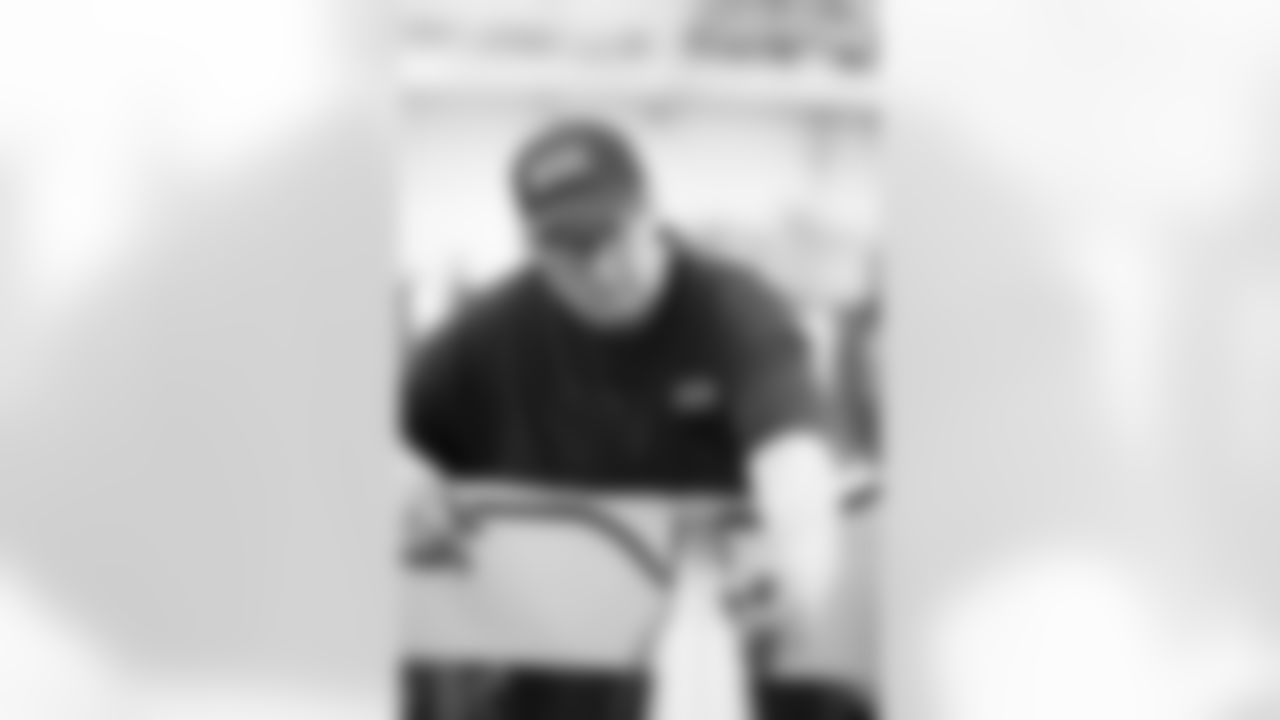
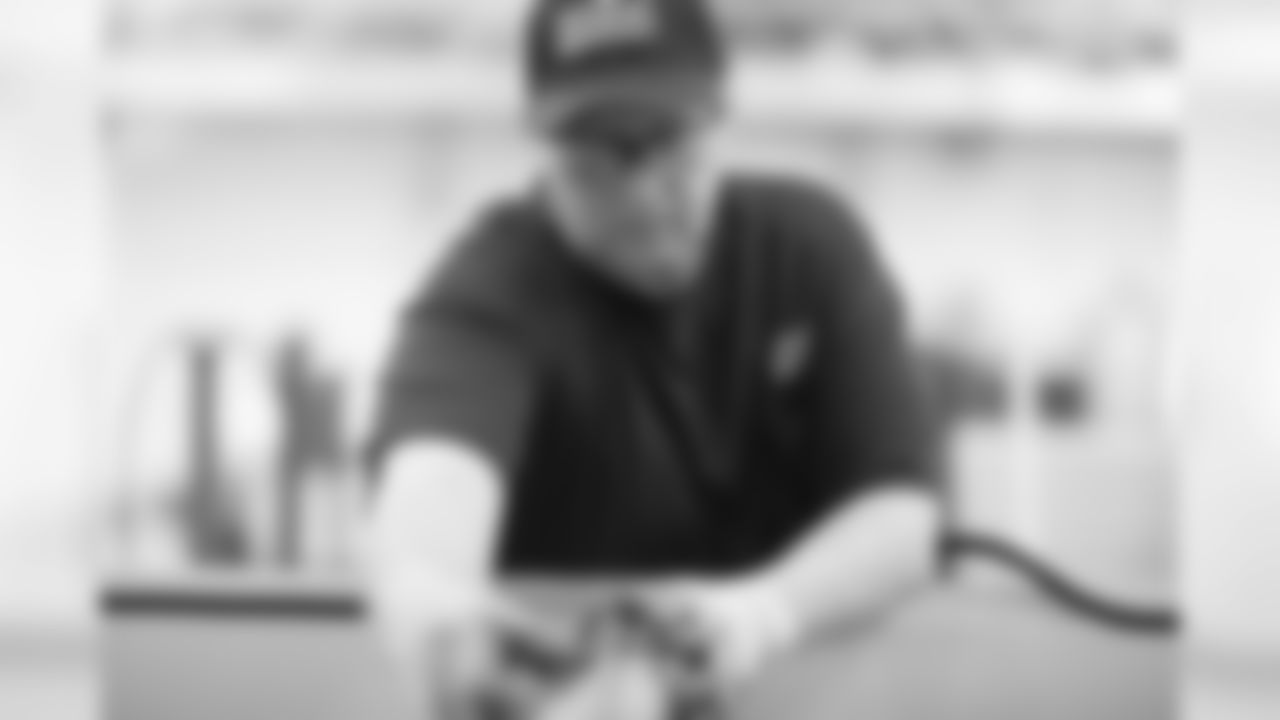
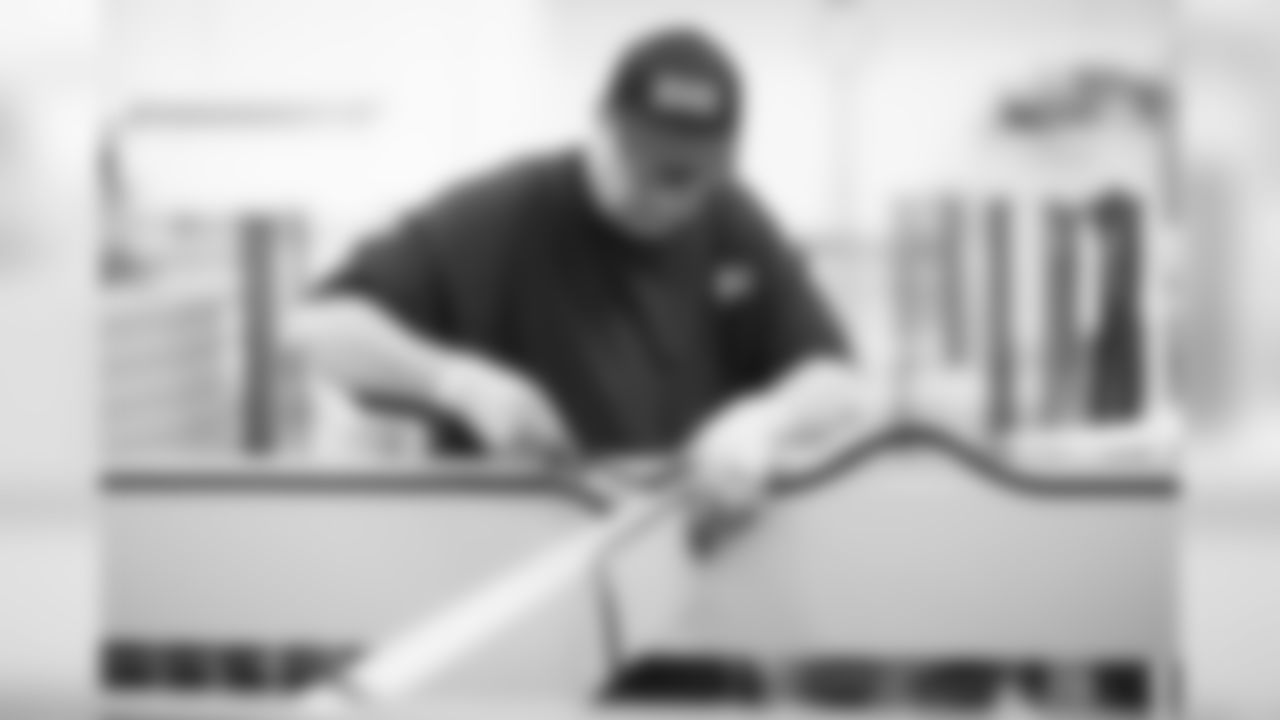
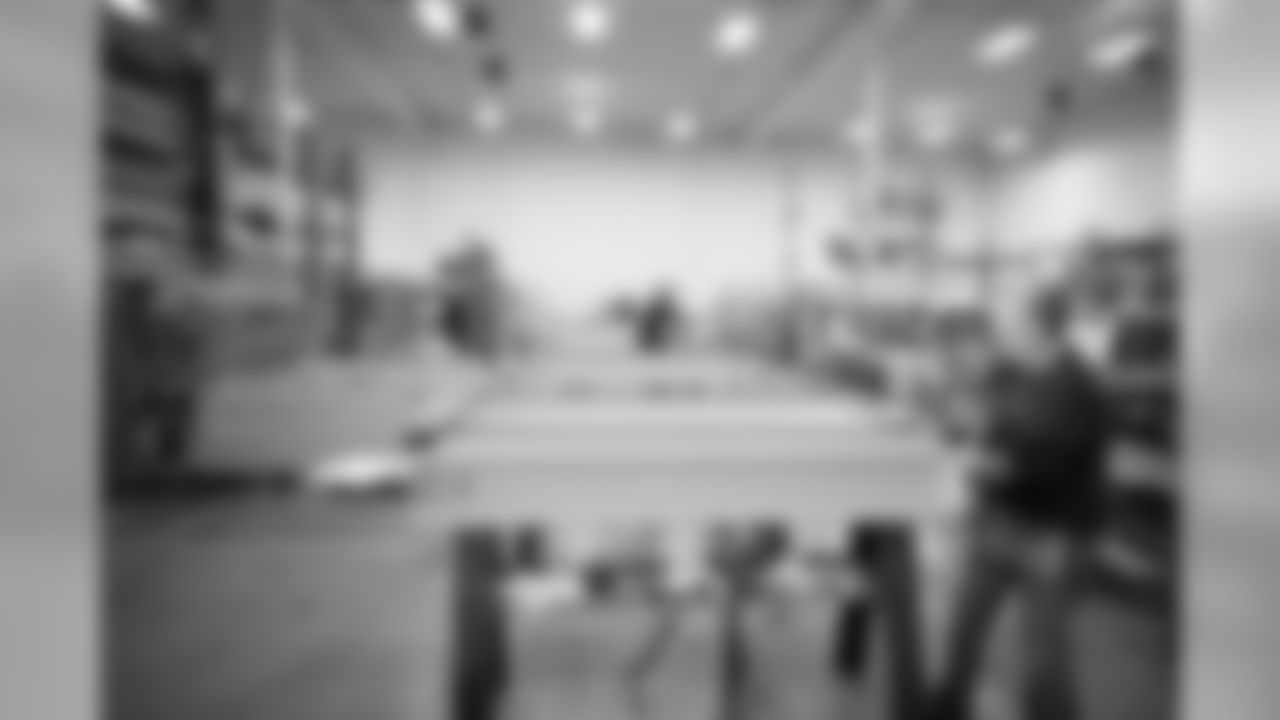
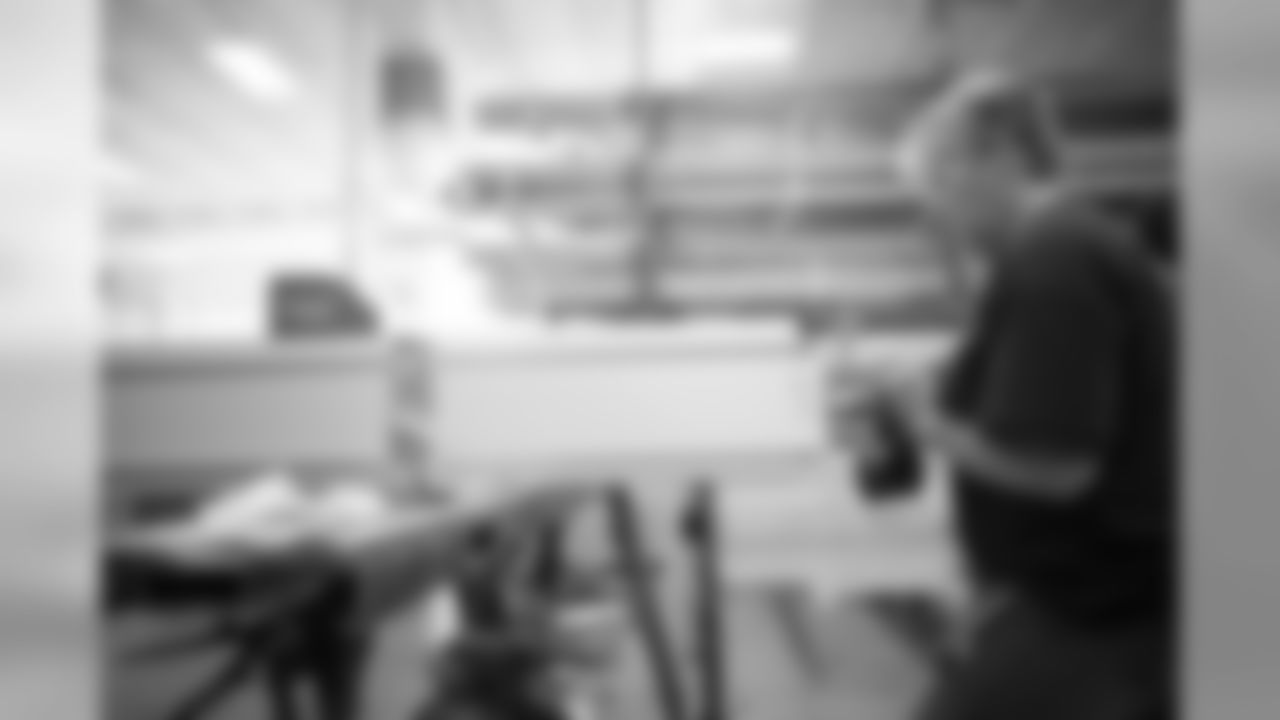
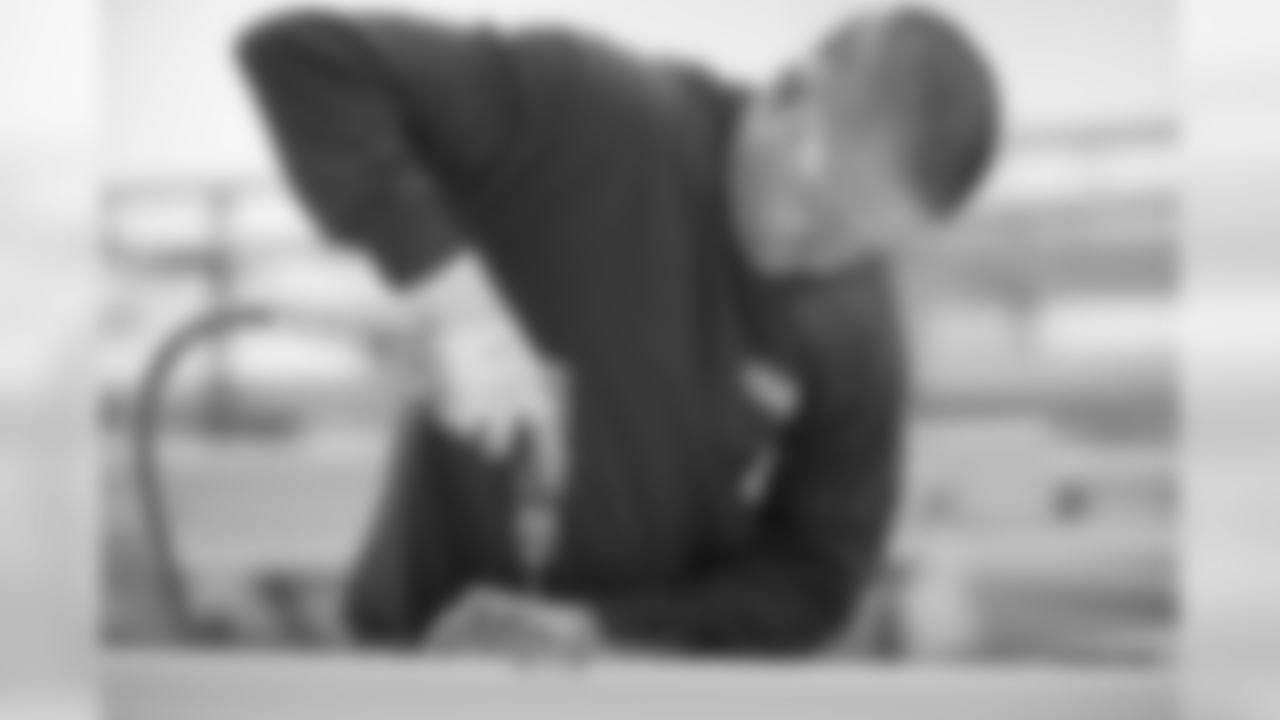
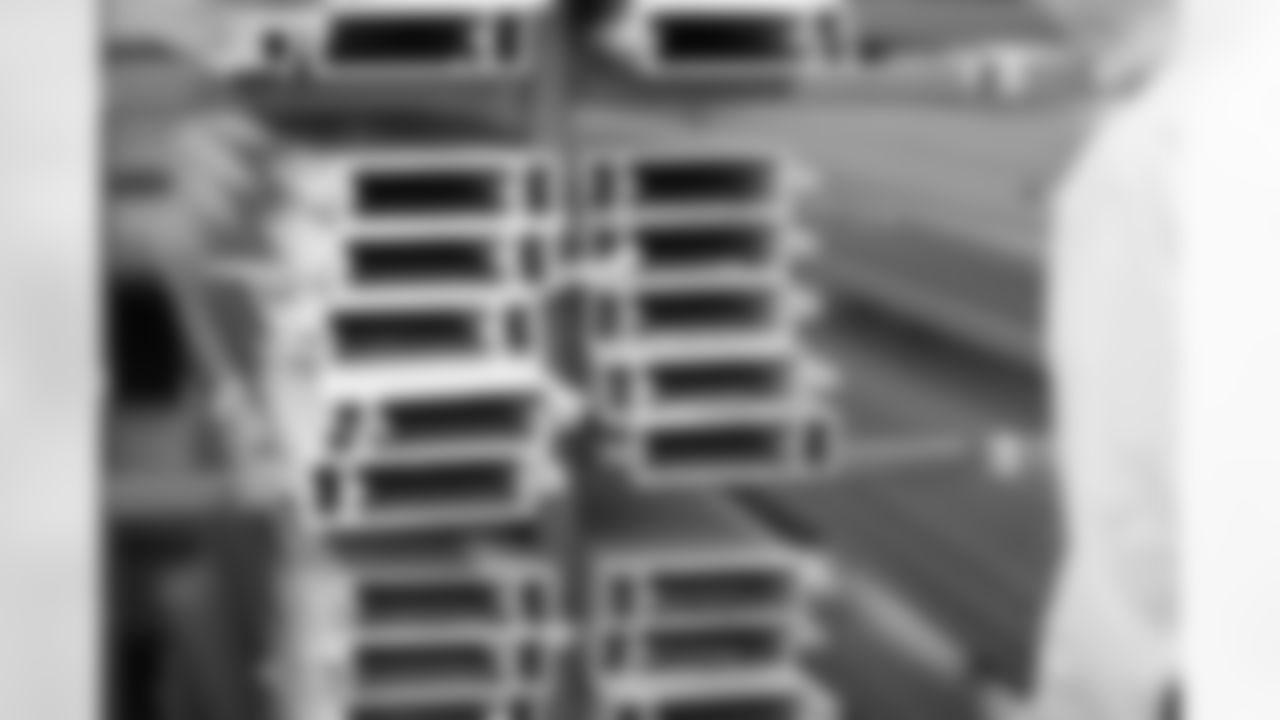
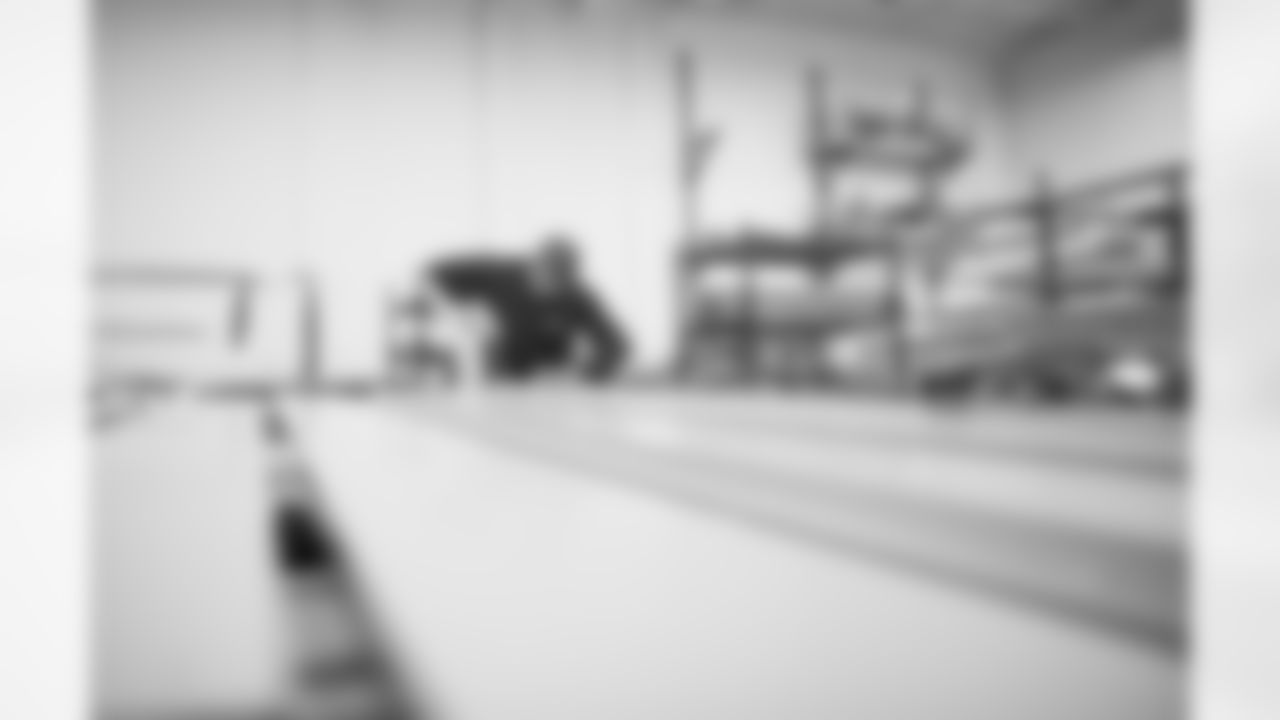
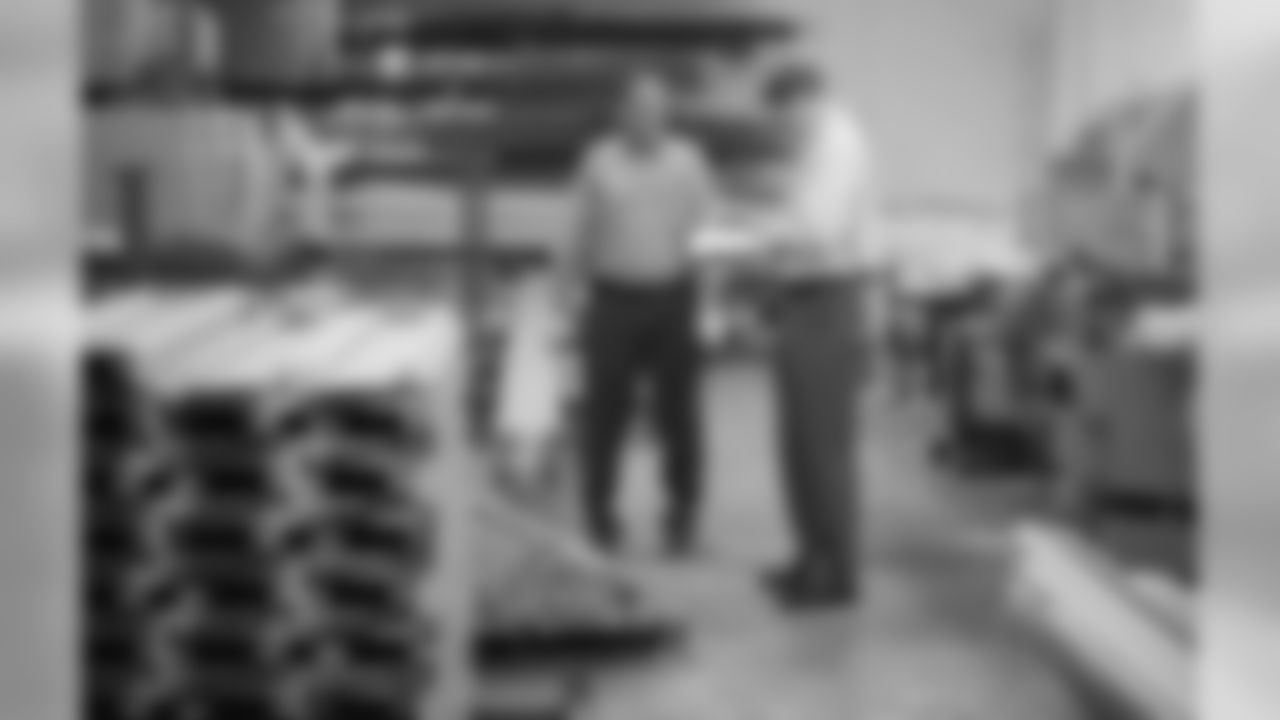
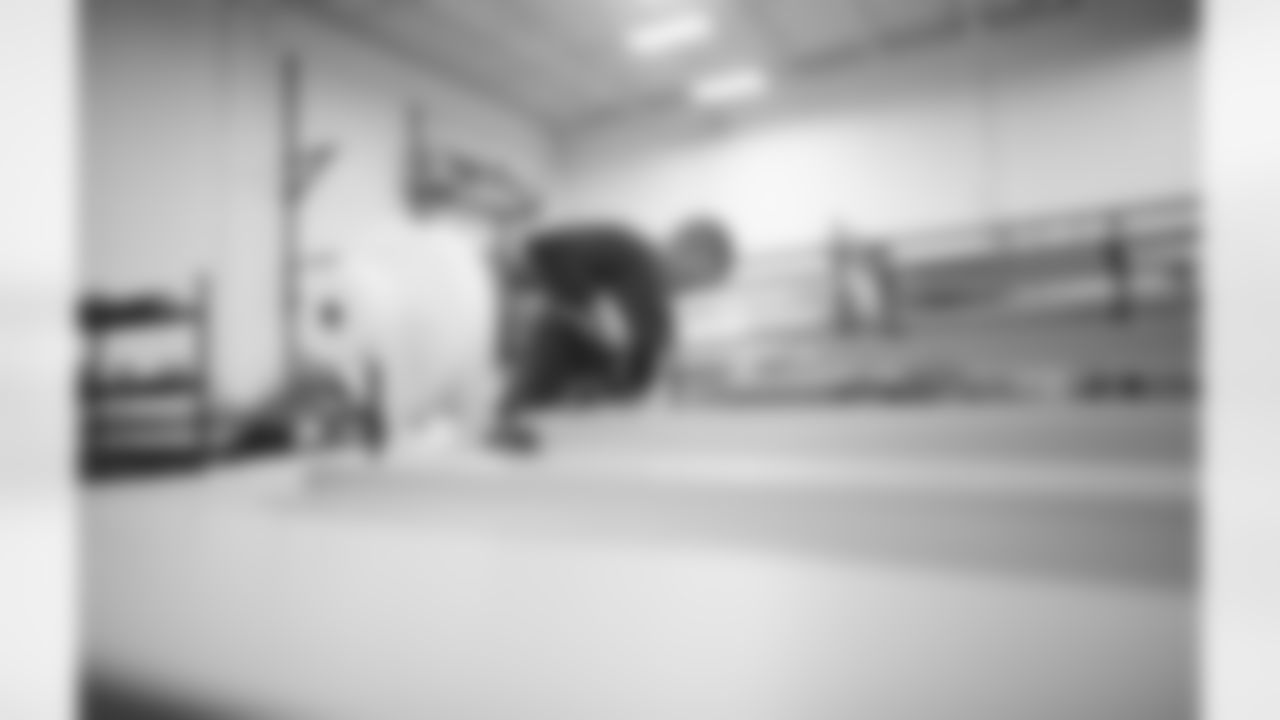
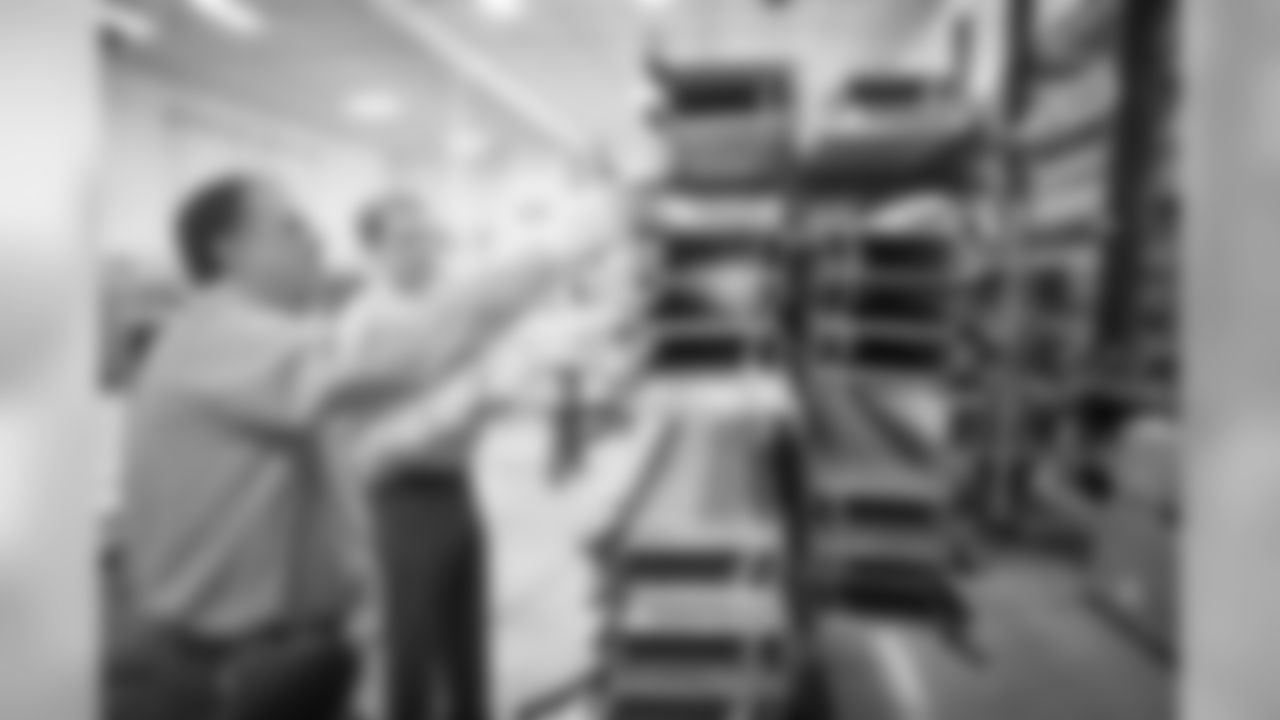
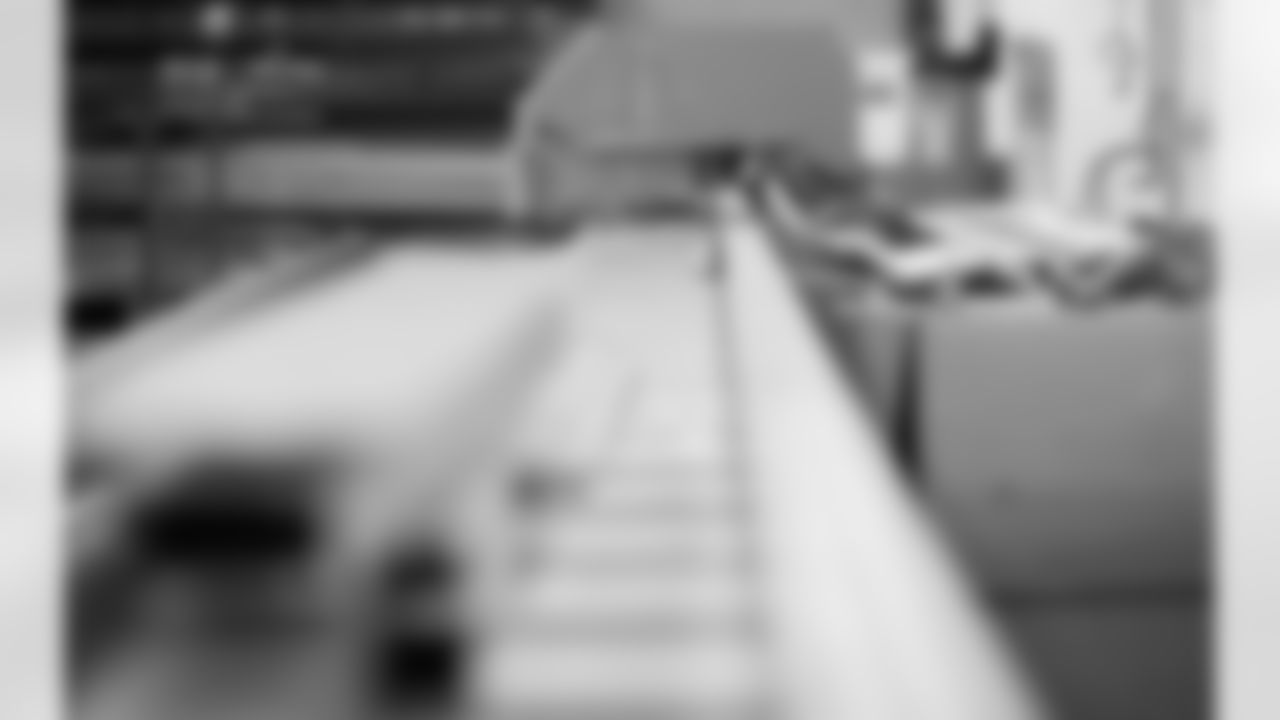
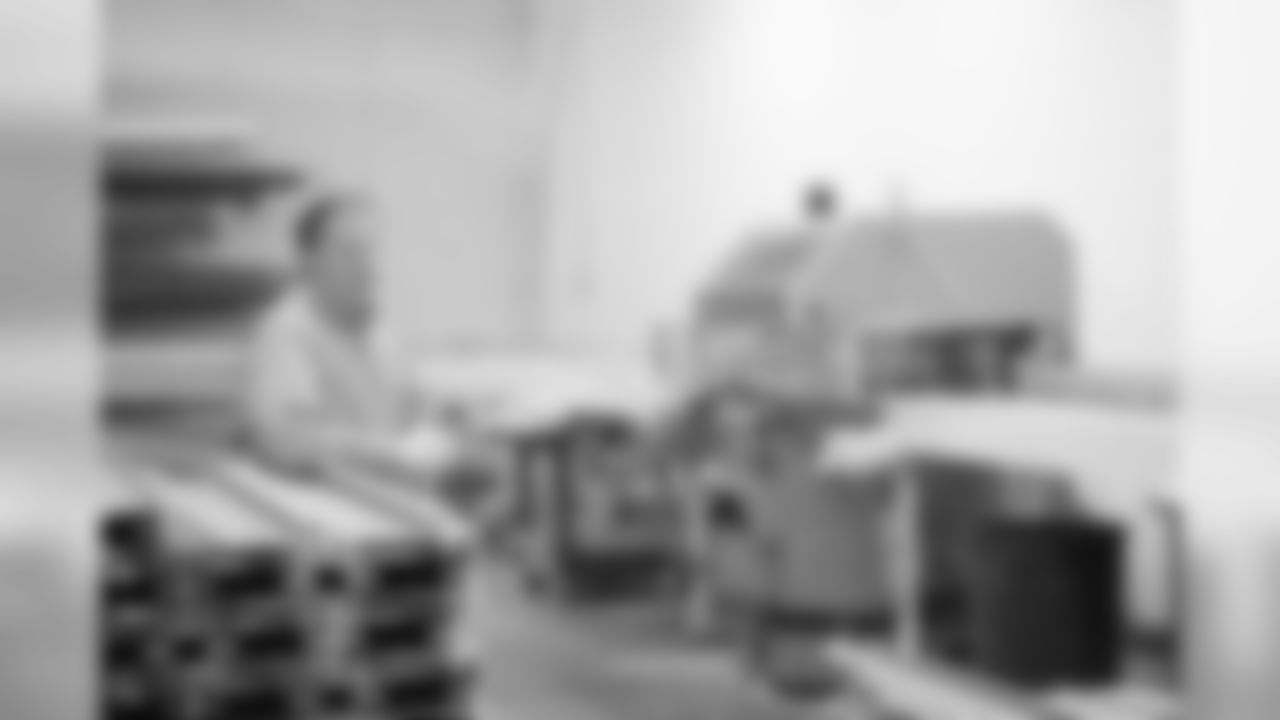
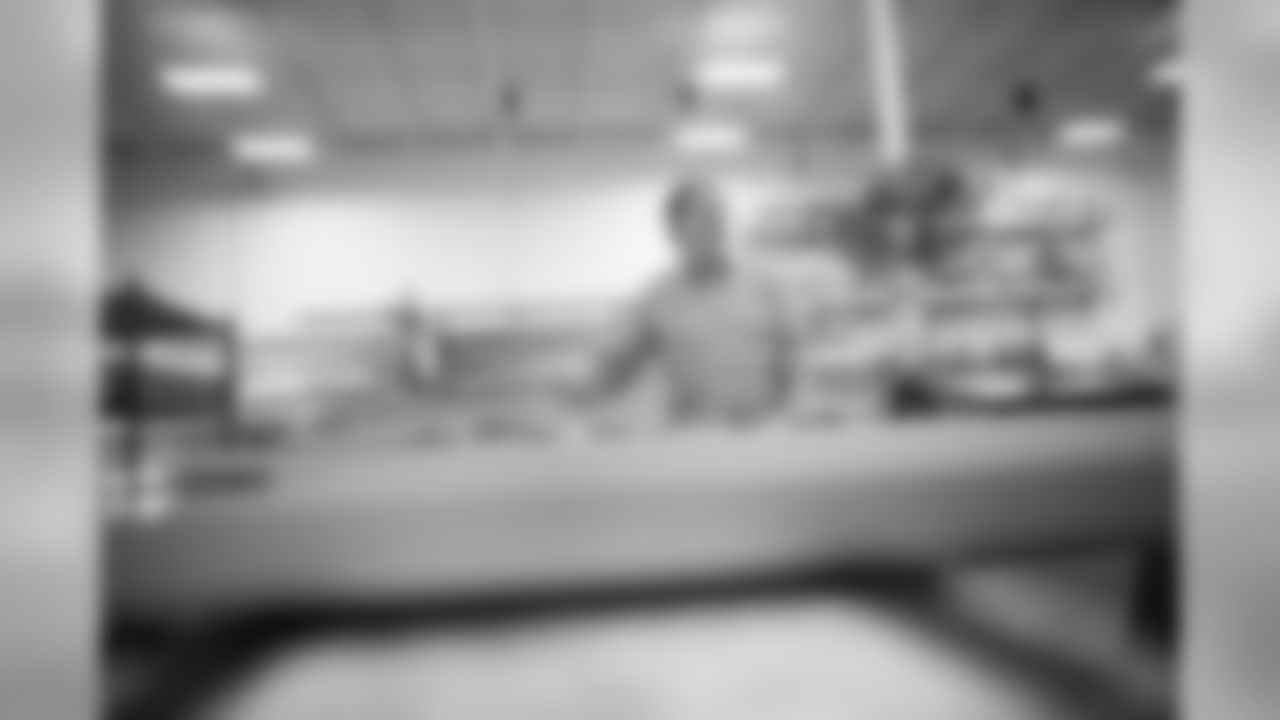
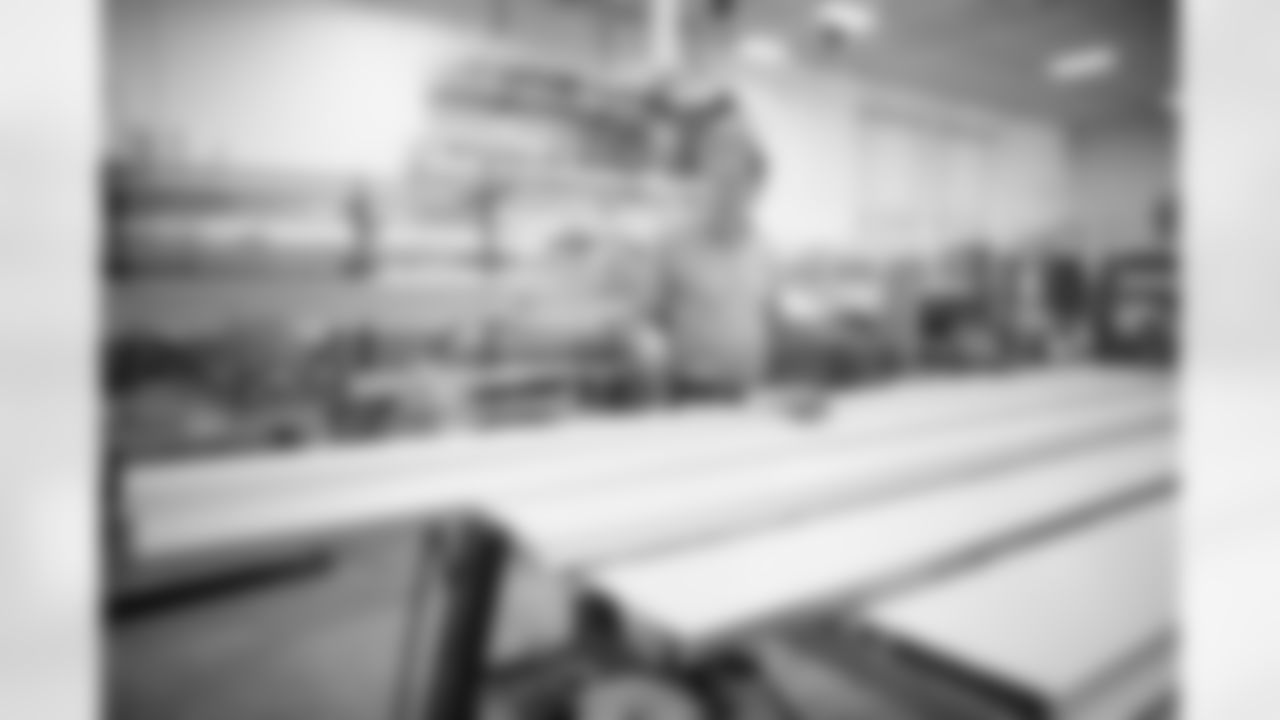
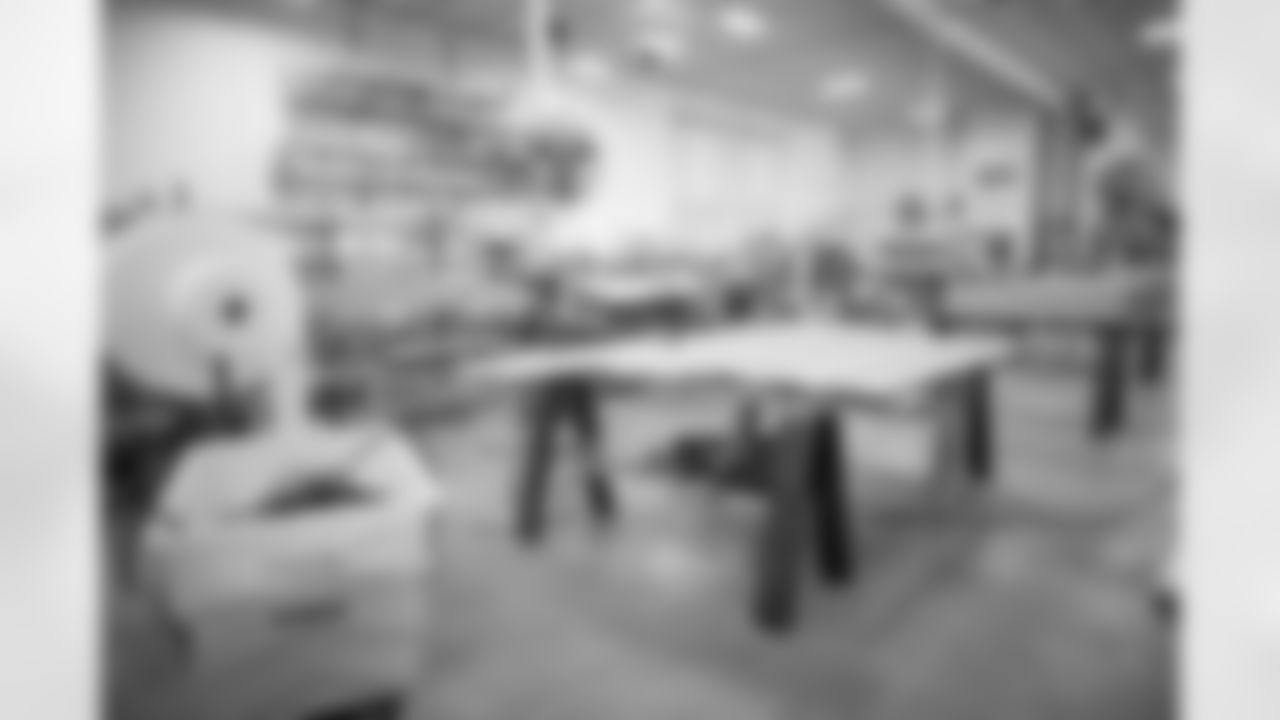
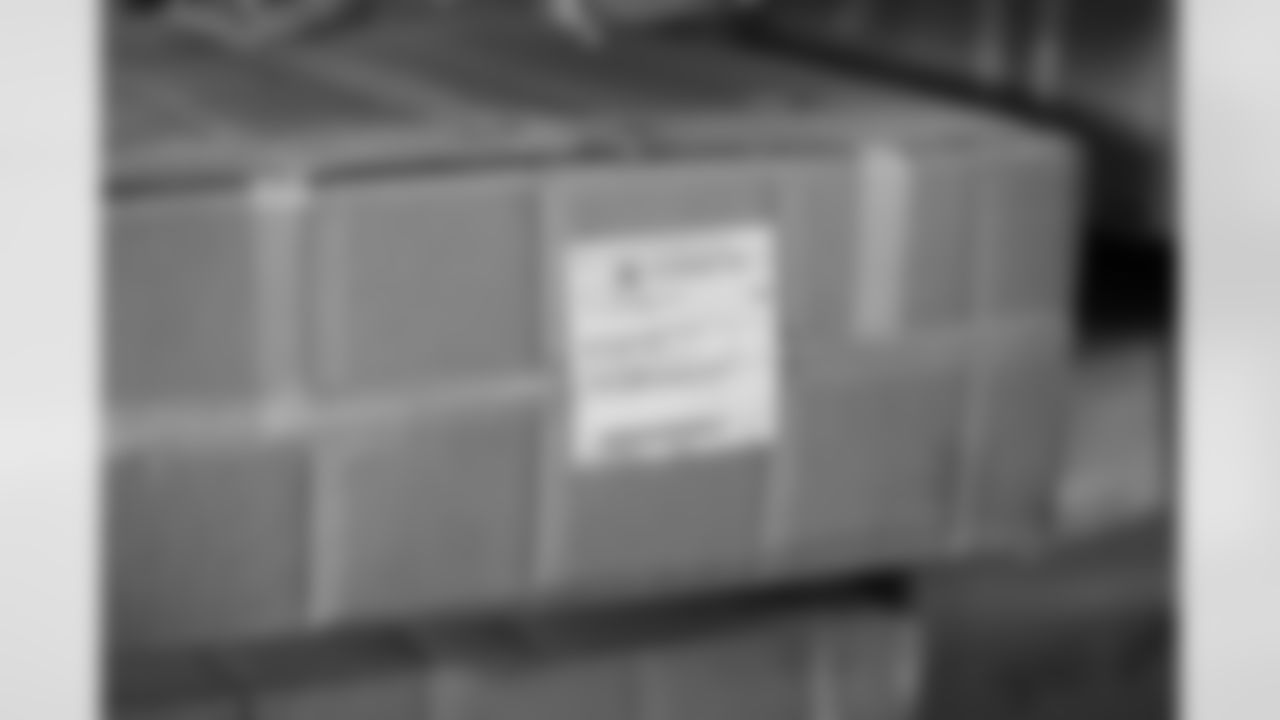
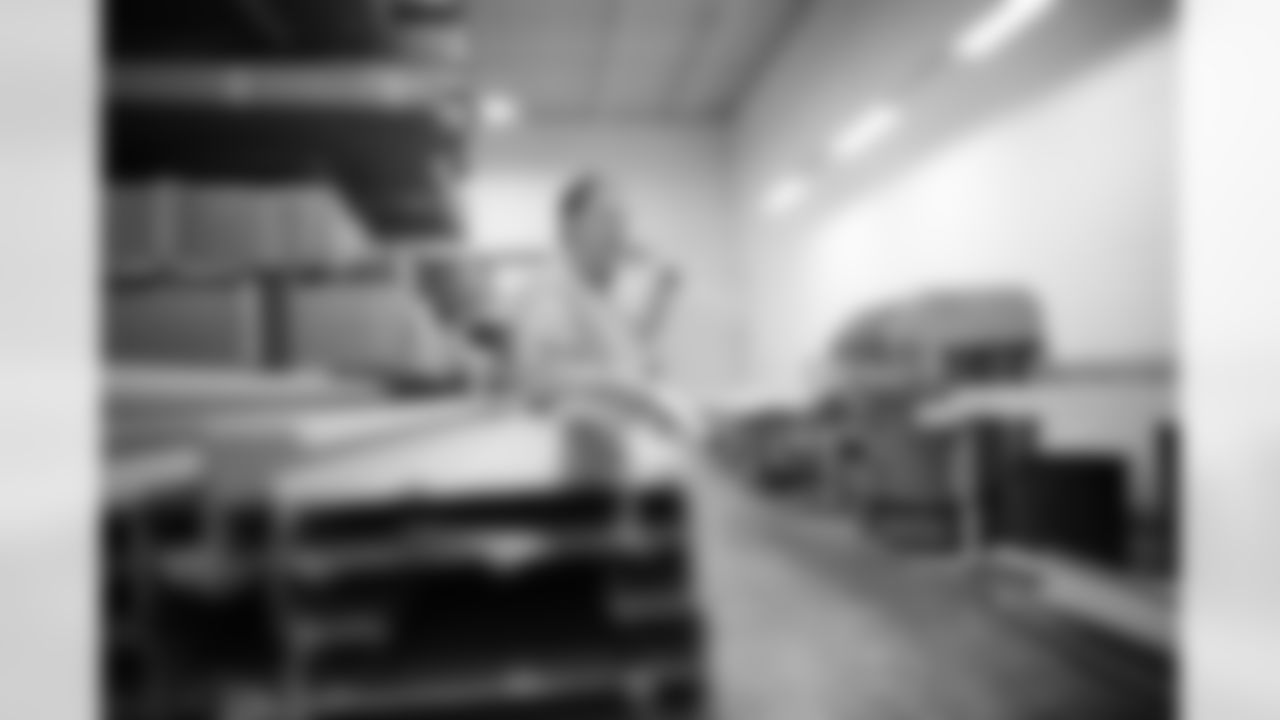
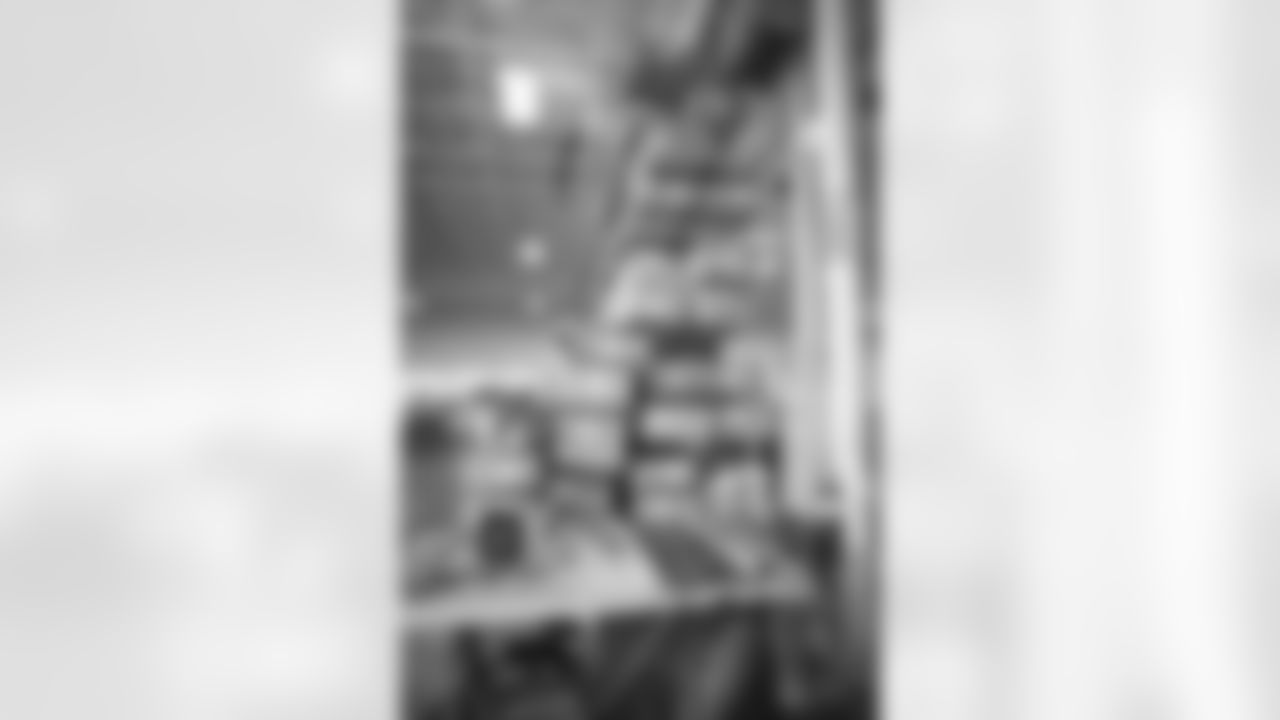
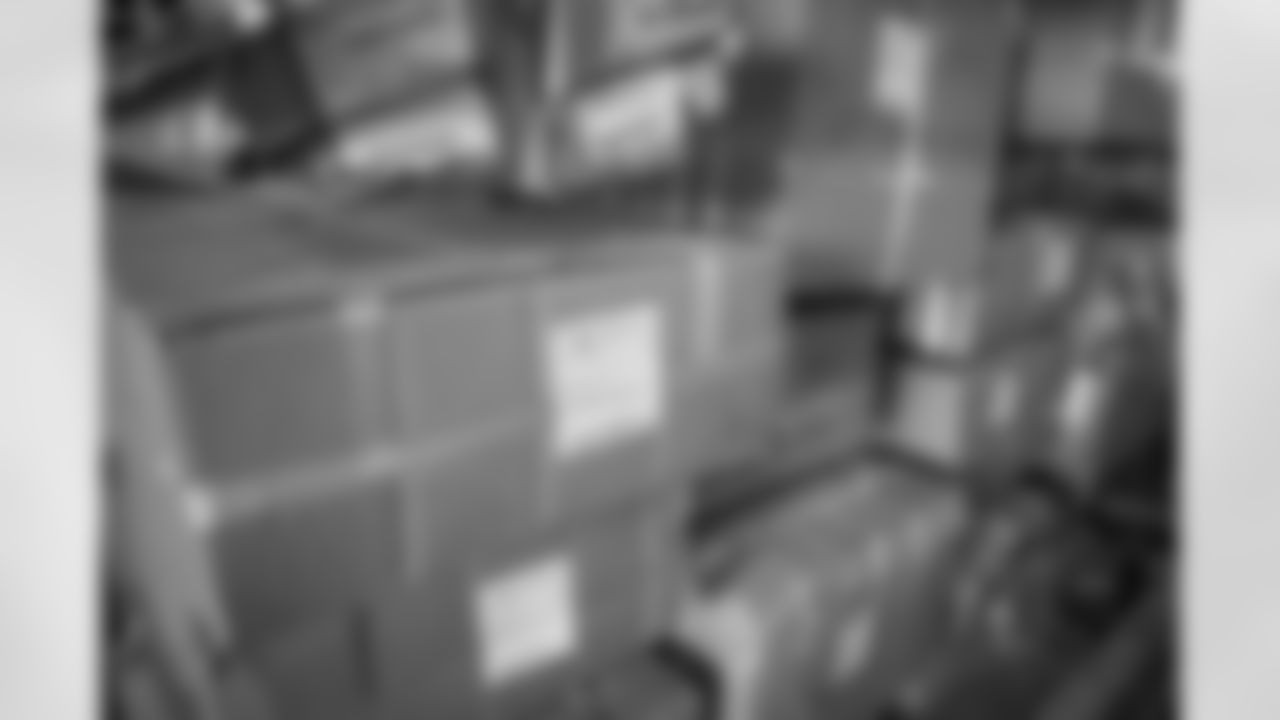
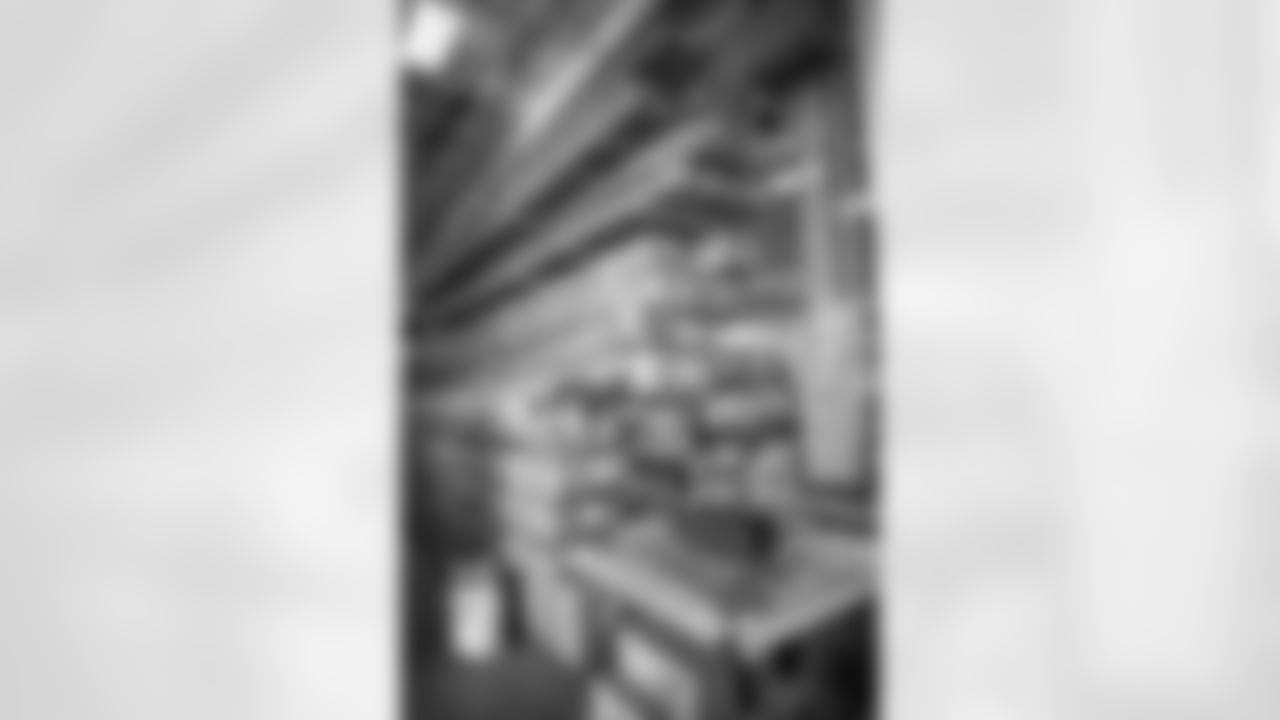
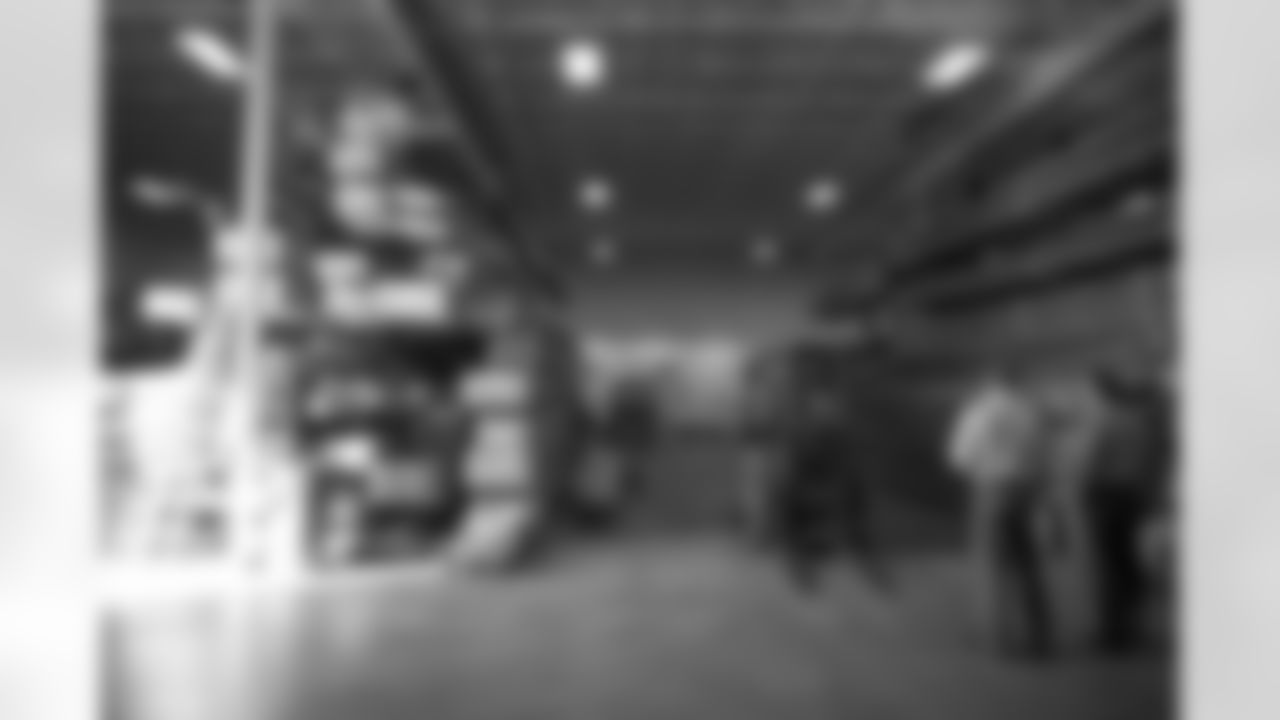
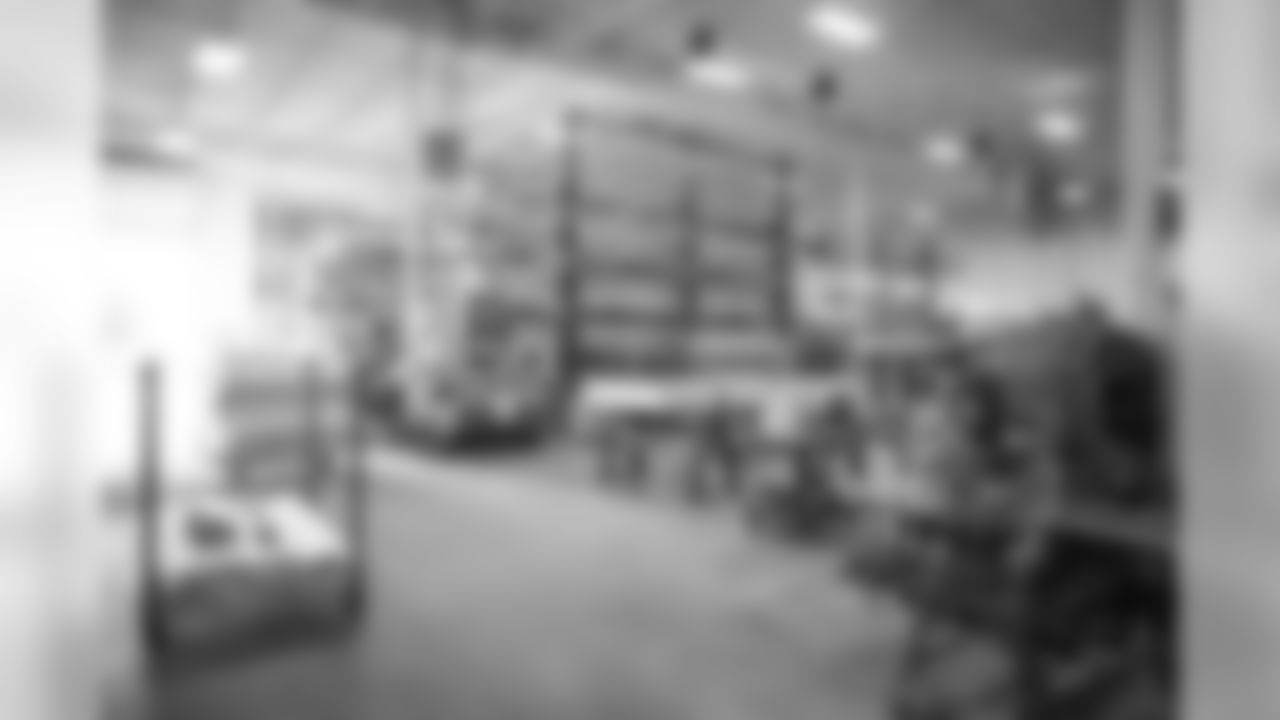
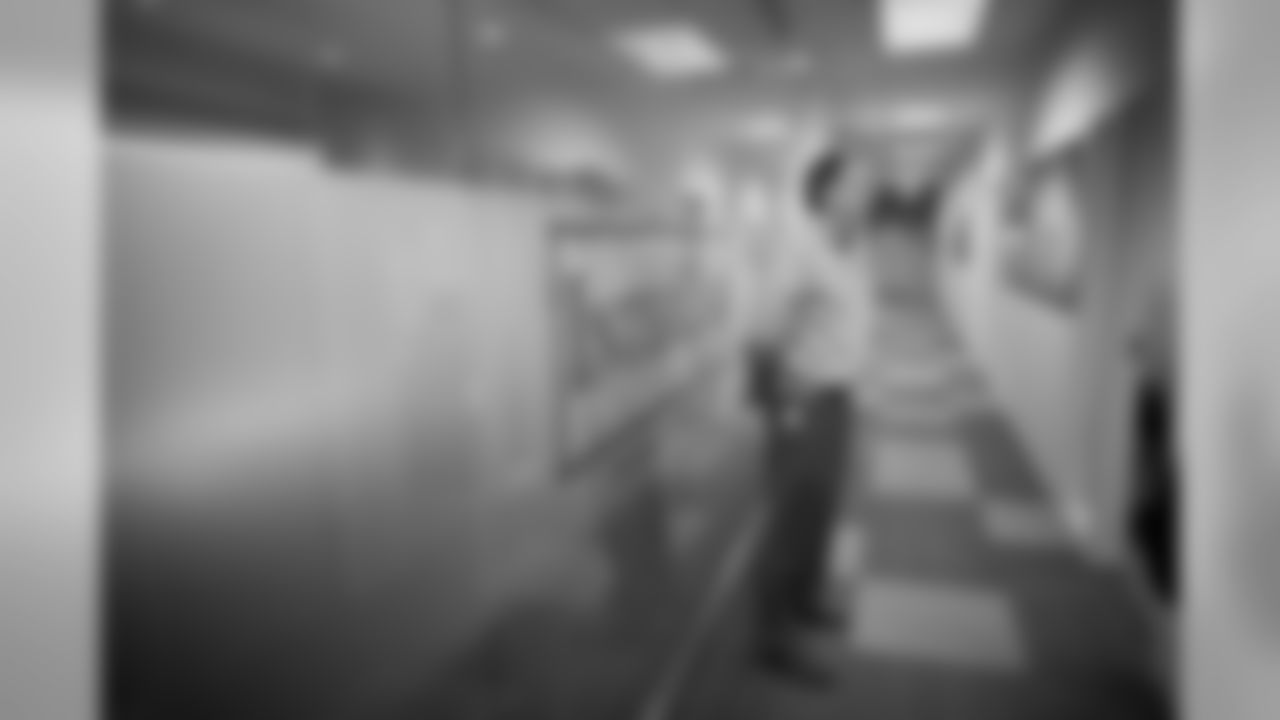
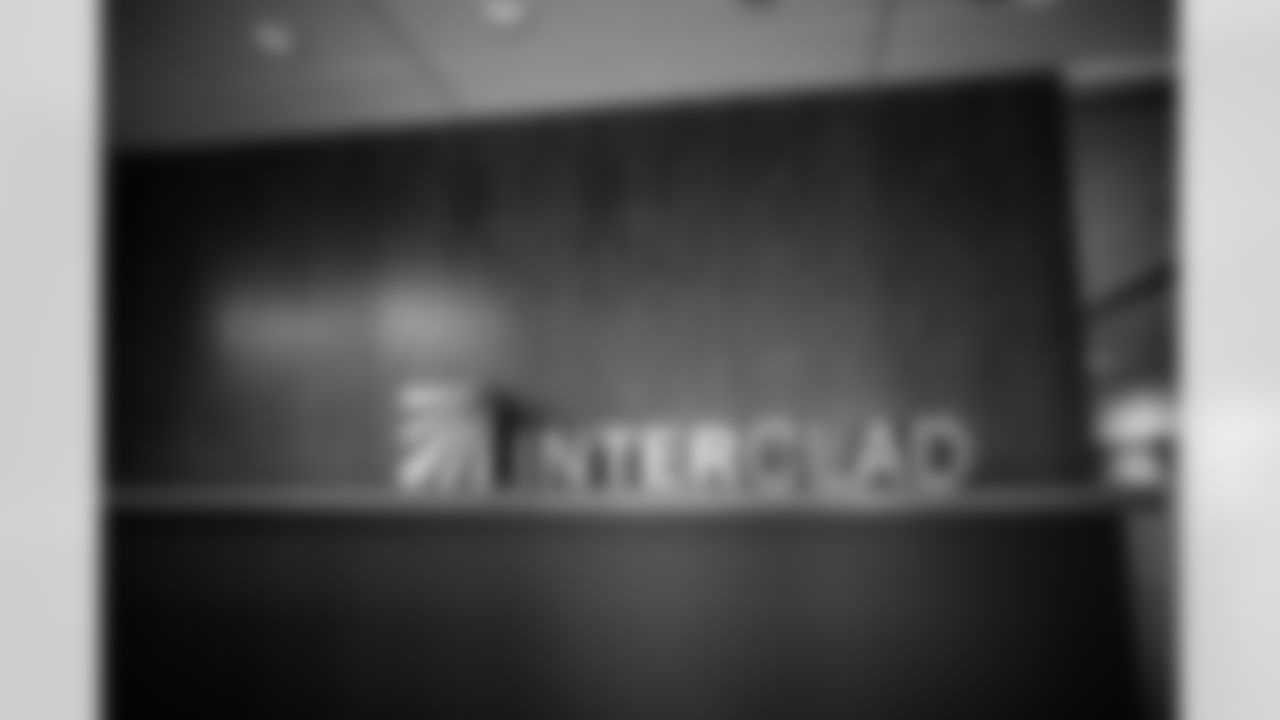
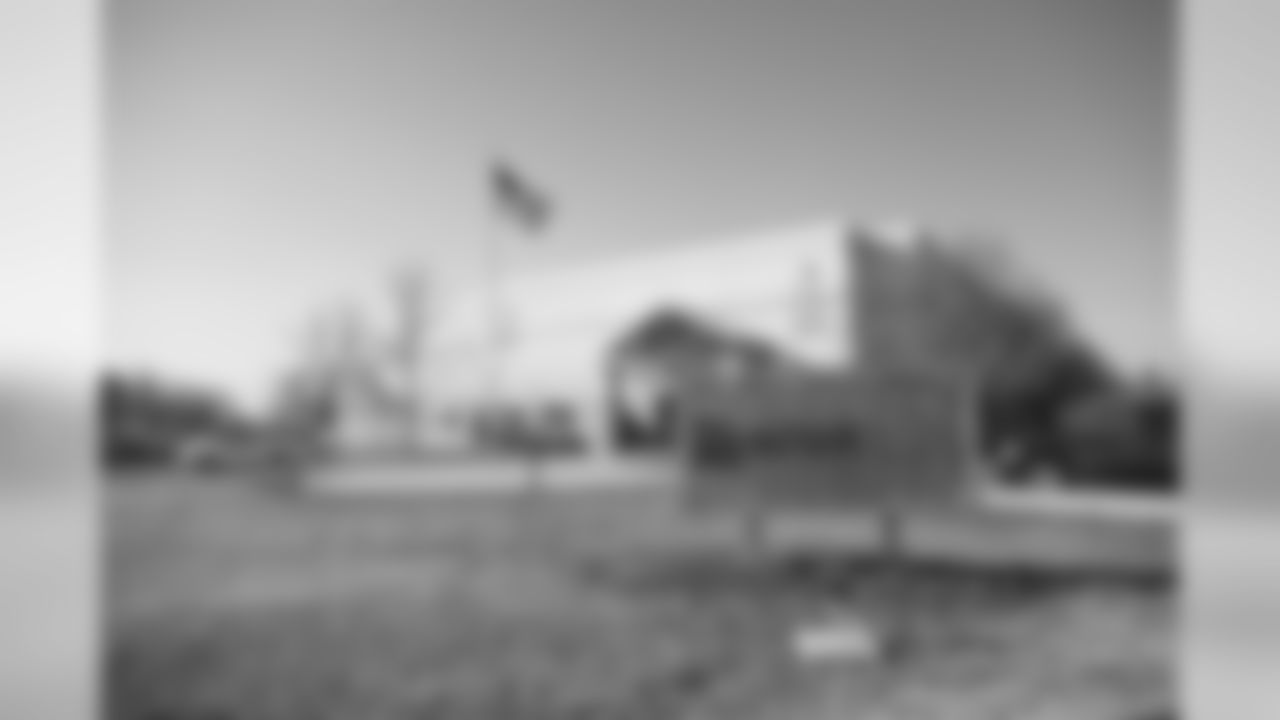
Now, as President and CEO of Brooklyn Park-based Egan Company, Malecha is helping usher in a new experience for football fans, one that will allow them to wear Vikings jerseys comfortably late into the season and have views of the Minneapolis skyline from the new Vikings stadium.
This duality will be possible thanks to a bold, iconic design from architecture firm HKS, executed by lead contractor Mortenson and subcontractors like Egan Company's business group InterClad, which is working on the curtain wall system of aluminum frames and glass. The system will form part of the building's skin and will allow light but not too much heat in, as well as shield fans from the harshest elements — frigid air, stiff winds and precipitation — of Minnesota's climate.
There were no signs of such brutality during an April 17 visit to InterClad when temps reached 73 degrees on the one-year anniversary of the last haul-off of Metrodome materials. The new stadium is **soaring past** its predecessor, and celebrated its **50-percent completion** mark last month.
Less than 15 miles northwest, an open garage door through which materials enter and completed frames exit, let in sunshine and warmth as Malecha and InterClad Senior Vice President Tim Woolworth led Vikings.com on a facility tour.
"The curtain wall keeps the outside elements out," Malecha said. "It's the skin of the building and can also keep the wind from coming in, but allow in the light. It really protects the occupants on the inside from the outside elements."
Six of the company's 18 fabrication employees are working full-time to produce the aluminum frames that were designed before InterClad began ordering the 180,000 square feet of glass that is being fabricated by Viracon at its Owatonna headquarters, 65 miles south of Minneapolis. As production intensifies, InterClad will assign 10 to 12 trade workers and employ a total of 24 employees in the fabrication shop.
"The curtain wall system we're using on this project is an aluminum system," Woolworth said. "It is what you call a pressure plate system. You've got your back member, which will be in varying depths, and the varying depths are designed for the wind loading. You don't want to use a narrow member. Otherwise, it's going to deflect too much, and glass will break. We've got a deeper system on this project.
"Once that framing is set, the glass is put up against the back gaskets, and then there is a pressure plate which also is preloaded with gasket," Woolworth continued. "That pressure plate gets attached with bolts to the back member, and those bolts are torqued to a certain inch pounds, and that is to keep the air and water out. Once the pressure plate is on, there's what we call beauty caps, snap covers that get snapped on to the pressure plate, and that's what you visually see from the exterior of the building for framing."
Emphasis is placed on optimization and organization throughout the project. The first helps production efficiency as long lengths of extrusions are trimmed into smaller pieces with an Emmegi miter saw that is kept on schedule by a computer system that automates the lengths of pieces cut. Organization enables the frames to be delivered to the correct locations at the site to maximize convenience and efficiency for installation crews. Codes printed on stickers and written in Sharpie (they won't be visible once frames are installed) sync with plans on-site, like a jigsaw puzzle with less rounded cuts and essential hints.
InterClad ordered the saw once it was awarded the contract for the stadium. It makes quick work of simple cuts, shrieking as toothy spinning metal cleanly rips through the aluminum. The saw also is capable of handling all the compound cuts that will make the stadium's unique and compelling geometry a reality.
"The Vikings stadium has more unique geometry than we've seen on past projects, to a larger scale," said Woolworth, an Iowa native who has been in the glazing business for 30 years. "We have had complex geometry before, but not to the percentage that we're seeing on this project. Through our (quality control) process, and our upfront work in the office, it's very critical that we provide proper fabrication packages with dimensions and details to the shop."
InterClad was launched by Egan Company in 1998 and is continuing to grow as glass curtain wall is proving its success at keeping out unwanted elements. That effectiveness and the aesthetic appeal have led to more frequent use as a design feature. The company also did the curtain wall for Target Field and for Target's Northern Campus corporate facility in Brooklyn Park.
"We had a great run on the Twins," Malecha said. "It was a really fun job for us and we were very proud to be on it. That really worked in our advantage to get the Vikings stadium. It's the same group with Mortenson. They knew us, we knew them, so we were really excited and we knew what we were going into, what kind of people we were going to be working with so it was really easy for us to want to chase and go after that job. For us to say we were part of (the Vikings stadium) is really cool for our people, so it was a very easy decision for us to want to be part of that."
The new Vikings stadium is the largest construction project in state history and one of the most challenging in InterClad's history because of the geometry.
"It tests us from a design, from a production standpoint, but honestly it's fun doing new projects," Malecha said. "It's fun working with new materials, and what's most fun about it is we get to see automatically what's going on in a building. When you're on the outside, that's what you see, that glass. Look at some of the prominent structures in the Twin Cities, they're glass-clad buildings and they look really cool."
Installation of the curtain wall system **began in March**, providing a significant milestone for InterClad.
"We've been at this for about 18 months. There's a lot of planning that goes on internally, working with the architects, working with the owners, working with the general contractor, Mortenson, so it has been very nice," Malecha said. "We've been waiting and waiting to get on-site and start installing our panels and glass, and we're just at the beginning, so we've got a long ways to go. It's been worth the wait, but it's time for us to get going and really get that glass installed."
Emotions will escalate, Woolworth said, and peak when the final components are placed.
"It's been exciting," Woolworth said. "It's even more exciting to get to the point where we can get on site and see everyone's hard work coming together in a finished product out in the field."
The stadium, which is on track to open in July 2016, is scheduled to be fully enclosed by November. It is already tabbed to host Super Bowl LII in 2018 and the NCAA men's basketball Final Four in 2019.
Fully enclosed is a particular point of pride for InterClad and the curtain wall installation crew.
"Water is not a glass guy's friend," Woolworth said. "The water is the biggest challenge during installation. We need to make sure we're putting in all the critical seals and that our field trade specialists are doing an excellent job of (quality controlling) it from their end out in the field."
Mock-ups of the curtain wall were built and transported to a specialized testing facility in Pennsylvania where a four-person crew verified performance against some of the same elements that led to Malecha's use of a snowmobile suit.
Having experienced the Vikings' first move indoors, Malecha is excited for the next transformation with help from the transparent curtain wall.
"Nothing to knock the Metrodome, but it's great to see the Twin Cities step into this century with a quality stadium," Malecha said. "I think it's going to be great for our state. It's a showpiece. It's something we can be very proud of, and with the NCAA Final Four, the Super Bowl, it fits so well."